Method for processing ultra-pure ferrite stainless steel by using ladle refining furnace to control carbon and nitrogen content
A ladle refining furnace and ladle refining technology, applied in the field of metallurgy, can solve problems such as steel reforming and product refining rate reduction, and achieve the effects of saving investment, being flexible and convenient to stop, and easy and flexible to implement
- Summary
- Abstract
- Description
- Claims
- Application Information
AI Technical Summary
Problems solved by technology
Method used
Image
Examples
Embodiment 1
[0041] When using the 30t EAF-AOD-LF-CC (electric arc furnace-argon oxygen decarburization furnace-ladle refining furnace-continuous casting) process to produce 409L ferritic stainless steel, when the electric arc furnace is smelted and passed through the argon oxygen decarburization furnace ( After AOD) refining, hoist the ladle to the LF station of the three-phase AC ladle refining furnace, and seat it on the ladle car, connect the bottom blowing pipeline and open the bottom blowing gas valve to test the gas. The ventilation brick has good air permeability, and the ladle car is driven Go to the heating station of the LF furnace and lower the ladle cover to keep a good seal between the ladle cover and the upper edge of the ladle. Then take a sample from the opening on the ladle cover, and take a sample from the temperature measurement port (T=1575°C), and send the sample to the laboratory for inspection and analysis. Add the weighed slag into the furnace from the alloy feedin...
Embodiment 2
[0044] Also adopt the technological process of embodiment 1, just change the gas ratio of blowing process into the mixed gas containing 20% coke oven gas and 80% argon, gas flow rate is 78m 3 / h·t steel, other operating procedures are basically unchanged.
[0045] Spray 20% coke oven gas + 80% Ar mixed gas into the hollow electrode. Due to the increase in the proportion of coke oven gas, the blowing flow rate increases, and the arc power increases by 2.2 times. After refining for 9 minutes, the carbon content in the steel decreases from 0.02%. To 0.0079%, the nitrogen content was reduced from 164ppm to 93ppm. Continue the gas blowing treatment until the end of refining, and the nitrogen content continues to decline during the gas blowing process. At the end of the LF treatment, the nitrogen content drops to 35ppm, and the carbon content in the steel also continues to drop from 0.0079% to 0.0025%.
Embodiment 3
[0047] The smelting process flow of embodiment 3 adopts 30t EAF-AOD-VOD-LF-CC (electric arc furnace-argon oxygen decarburization furnace-vacuum oxygen blowing decarburization furnace-ladle refining furnace-continuous casting) process, and the production steel type is 409L iron Body stainless steel. After the molten steel initially smelted in the electric furnace is refined by AOD, the steel is poured into the ladle and sent to VOD for refining. At the end of VOD treatment, the carbon content in the steel reaches 29ppm and the nitrogen content is 56ppm. The molten steel after VOD refining is hoisted into the LF station for heating and composition fine-tuning.
[0048] In the LF refining process of the three-phase AC ladle refining furnace, the basic operation of this furnace is similar to the operation steps of Example 1. During the refining and electrification process of this furnace, 5% coke oven gas + 95% coke oven gas is injected from the graphite electrode hole The mixed ...
PUM
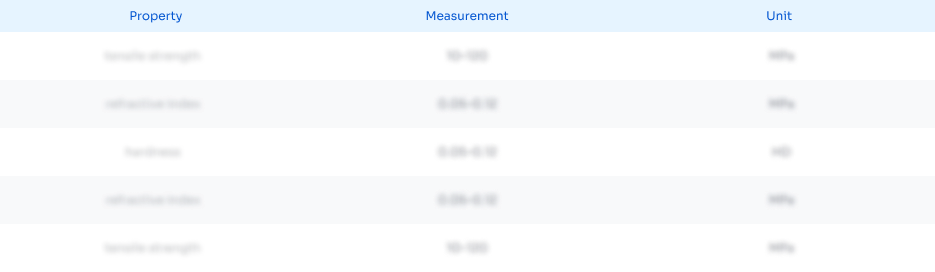
Abstract
Description
Claims
Application Information

- R&D
- Intellectual Property
- Life Sciences
- Materials
- Tech Scout
- Unparalleled Data Quality
- Higher Quality Content
- 60% Fewer Hallucinations
Browse by: Latest US Patents, China's latest patents, Technical Efficacy Thesaurus, Application Domain, Technology Topic, Popular Technical Reports.
© 2025 PatSnap. All rights reserved.Legal|Privacy policy|Modern Slavery Act Transparency Statement|Sitemap|About US| Contact US: help@patsnap.com