Fluorescent powder slurry materialfor plasma display and forming method on shadow mask
A plasma and phosphor technology, used in chemical instruments and methods, fluorescent layers, luminescent materials, etc., can solve the problems of poor thixotropy of phosphor paste, improve dispersibility and suspension, good adhesion, easy-to-achieve effects
- Summary
- Abstract
- Description
- Claims
- Application Information
AI Technical Summary
Problems solved by technology
Method used
Image
Examples
Embodiment 1
[0024] First, formulate the blue phosphor paste and make it on the shadow mask:
[0025] The organic resin ethyl cellulose 3 g, SiO 2 2 grams of nano-powder and 45 grams of organic solvent terpineol were mixed and fully dispersed, and the organic carrier was prepared under stirring in a water bath, and then 50 grams of blue phosphor particles were fully dispersed in it to form a blue phosphor slurry.
[0026] The blue phosphor paste prepared above is printed on the shadow mask by screen printing method. After printing, the shadow mask is placed on the platform and leveled for 10-15 minutes, and observed under a microscope. The printing material is full, no blocking holes, no bubbles. Directly put the shadow mask into an oven at 150°C to 170°C for drying, and the drying time is 15 to 20 minutes. After drying, put it under a microscope to observe the condition of the phosphor film layer. It can be seen that the two walls and bottom of the shadow mask hole are uniformly attache...
Embodiment 2
[0035] First, formulate the blue phosphor paste and make it on the shadow mask:
[0036] The organic resin ethyl cellulose 6g, SiO 2 3 grams of nano-powder and 51 grams of organic solvent terpineol were mixed and fully dispersed, and an organic carrier was prepared under stirring in a water bath, and 40 grams of blue phosphor particles were fully dispersed in it to form a blue phosphor slurry.
[0037]The blue phosphor paste prepared above is printed on the shadow mask by screen printing method. After printing, the shadow mask is placed on the platform and leveled for 10-15 minutes, and observed under a microscope. The printing material is full, no blocking holes, no bubbles. Directly put the shadow mask into an oven at 150°C to 170°C for drying, and the drying time is 15 to 20 minutes. After drying, put it under a microscope to observe the condition of the phosphor film layer. It can be seen that the two walls and bottom of the shadow mask hole are uniformly attached to the...
PUM
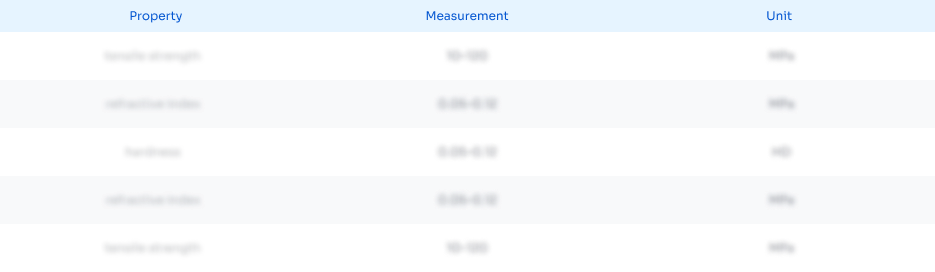
Abstract
Description
Claims
Application Information

- R&D
- Intellectual Property
- Life Sciences
- Materials
- Tech Scout
- Unparalleled Data Quality
- Higher Quality Content
- 60% Fewer Hallucinations
Browse by: Latest US Patents, China's latest patents, Technical Efficacy Thesaurus, Application Domain, Technology Topic, Popular Technical Reports.
© 2025 PatSnap. All rights reserved.Legal|Privacy policy|Modern Slavery Act Transparency Statement|Sitemap|About US| Contact US: help@patsnap.com