Method for manufacturing elastic conductive cloth
A manufacturing method and elastic conductive technology, which is applied in the field of conductive cloth, can solve problems such as wear or damage, affecting conductive performance, electromagnetic wave shielding performance and weather resistance, and poor thickness accuracy.
- Summary
- Abstract
- Description
- Claims
- Application Information
AI Technical Summary
Problems solved by technology
Method used
Examples
Embodiment 1
[0031] 1. Weave polyester fibers with a warp of 20 denier / 24 fibers, a weft of 30 denier / 12 fibers, a warp density of 189 threads / inch and a weft density of 125 threads / inch, and weave it into a plain woven fabric with a thickness of about 0.081mm ;
[0032] 2. Desizing, scouring, cleaning, and heat setting of the plain woven fabric; heat calendering conditions with a calender: temperature 180°C, pressure 100daN / cm, speed 30M / min, heat calendering twice on the same side, and become a thickness of 0.05 mm plain weave;
[0033] 3. The 0.05mm plain woven fabric and the 3mm polyurethane foam resin are sintered and welded to form an elastic fabric substrate with a thickness of 2.05mm, which is sintered to bond the fabric substrate after melting the polyurethane foam resin by flame to 1mm;
[0034] 4. Uniformly disperse 40% of water-based modified polyester resin and 3% of titanium dioxide powder in the aqueous solution, impregnate-pressure absorption rate of 60% (pressure absorpti...
Embodiment 2
[0040] Polyester fiber flat woven fabric, the same as the steps 1 to 7 of , the elastic conductive cloth material is subjected to flame-retardant and antifouling composite functional processing, impregnation-pressure suction processing conditions: water-based modified polyester resin 20 % + phosphorus flame retardant 30%, liquid absorption rate 80%, drying at 120°C for 2 minutes, aging at 180°C for 1 minute, to obtain a non-halogen flame-retardant electromagnetic wave shielding elastic conductive fabric with a thickness of 0.5mm.
Embodiment 3
[0042] 1. Weave polyester fibers with a warp of 20 denier / 24 fibers, a weft of 30 denier / 12 fibers, a warp density of 189 threads / inch and a weft density of 125 threads / inch, and weave it into a plain woven fabric with a thickness of about 0.081mm ;
[0043] 2. Desizing, scouring, cleaning, and heat setting of the plain woven fabric; heat calendering conditions with a calender: temperature 180°C, pressure 100daN / cm, speed 30M / min, heat calendering twice on the same side, and become a thickness of 0.05 mm plain weave;
[0044] 3. The 0.05mm plain woven fabric and the 3mm polyurethane foaming resin are coated and adhered to the engraving roller adhesive resin part area to form an elastic fabric substrate with a thickness of 3.05mm. The engraving roller coating condition: modified polyester resin adhesion agent, viscosity 2000cps, coating coverage area 60% dot coating;
[0045] 4. Disperse 40% of water-based modified polyester resin and 3% of titanium dioxide powder evenly in t...
PUM
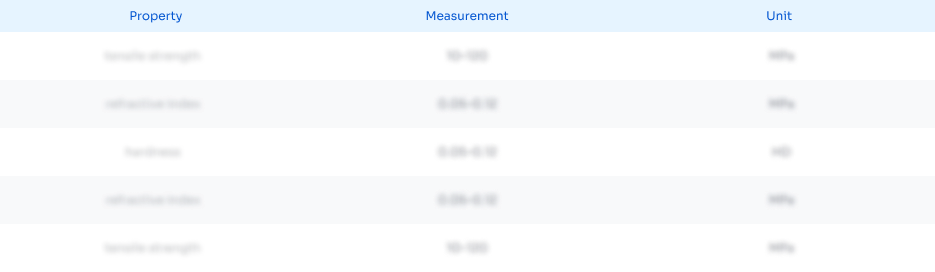
Abstract
Description
Claims
Application Information

- R&D Engineer
- R&D Manager
- IP Professional
- Industry Leading Data Capabilities
- Powerful AI technology
- Patent DNA Extraction
Browse by: Latest US Patents, China's latest patents, Technical Efficacy Thesaurus, Application Domain, Technology Topic, Popular Technical Reports.
© 2024 PatSnap. All rights reserved.Legal|Privacy policy|Modern Slavery Act Transparency Statement|Sitemap|About US| Contact US: help@patsnap.com