Friction plate, and its uses, production process and dedicated mould
A friction plate and mold technology, which is applied in the direction of friction shock absorber, etc., can solve the problems of easy wear, the surface of the friction plate is easy to break, fall off, affect the service life of the friction plate, etc., and achieve the effect of improving wear resistance
- Summary
- Abstract
- Description
- Claims
- Application Information
AI Technical Summary
Problems solved by technology
Method used
Image
Examples
Embodiment 1
[0030] Example 1: The embodiment of the present invention provides a friction plate, including glass cloth and a wear-resistant layer, the wear-resistant layer contains the following components and weight percentages: 15-30 parts of polyimide resin; 1.5 parts of mica iron oxide -3 parts; 4-8 parts of copper fiber; 10-17 parts of graphite; 1-5 parts of friction powder; 1.5-3 parts of magnesium oxide; 1-4 parts of petroleum coke; -2 parts; 2-15 parts of silica fume; 1-12 parts of short glass fiber; 2-12 parts of molybdenum disulfide; 1-10 parts of natural cellulose fiber.
[0031] Tests have proved that the friction plate made of the above raw materials has wear resistance, low wear, appropriate friction coefficient, excellent fatigue resistance, corrosion resistance, high vibration damping, good shock absorption, and good impact resistance. Performance, good weather resistance, can be used in an environment with large temperature changes for a long time, very suitable for the en...
Embodiment 2
[0036] Embodiment 2: The specific embodiment of the present invention also provides a production process for preparing the friction plate in Example 1. The raw materials of the friction plate in this embodiment can be weighed according to the specific gravity of the raw materials in Example 1. The production of this embodiment The process includes the following steps:
[0037] Fully mix and dry the raw materials of the wear-resistant layer to make wear-resistant materials; the glass cloth and 180g-300g wear-resistant materials are pressed and formed after exhausting 6-15 times and holding pressure for 20-60 minutes;
[0038] The formed friction plate is put into a special curing furnace and cured at a temperature of 180°C-230°C for 3-8 hours to form a friction plate.
[0039] In actual production, after the above steps are completed, the friction plate can also be cured, polished, drilled, marked and other post-processing. Make the performance of the friction plate more promi...
Embodiment 3
[0040] Embodiment 3: As shown in Figure 1, the specific embodiment of the present invention also provides a kind of special mold of friction plate, and this mold comprises mold cavity 2, outer mold body 10, fixed upper pressure head 1 and bottom plate 11, fixed upper pressure The head 1 cooperates with the film cavity 2 to press the friction plate. The mold also includes a plurality of movable lower pressure heads 7 and at least one movable upper pressure head 3. The movable upper pressure head 3 and the movable lower pressure head 7 can move in the mold cavity 2 and Cooperate with the fixed upper pressure head 1 to press the friction plate, the positional relationship between the movable upper pressure head, the movable lower pressure head, the fixed upper pressure head and the bottom plate from top to bottom or from left to right is fixed upper pressure head, movable lower pressure head , Active upper pressure head, movable lower pressure head, bottom plate. Since the mold i...
PUM
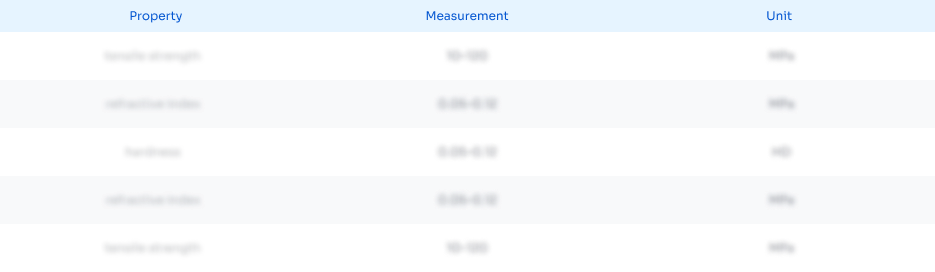
Abstract
Description
Claims
Application Information

- R&D Engineer
- R&D Manager
- IP Professional
- Industry Leading Data Capabilities
- Powerful AI technology
- Patent DNA Extraction
Browse by: Latest US Patents, China's latest patents, Technical Efficacy Thesaurus, Application Domain, Technology Topic, Popular Technical Reports.
© 2024 PatSnap. All rights reserved.Legal|Privacy policy|Modern Slavery Act Transparency Statement|Sitemap|About US| Contact US: help@patsnap.com