Surface modifier for transfer printing with dispersive cotton fabric dye and its pre-treatment method
A technology of surface modifiers and disperse dyes, which is applied in transfer printing, textile material processing, liquid/gas/steam textile material processing, etc. It can solve the problems of water absorption and air permeability decline, strength and color fastness decline, printing fabrics To solve the problem of dark color and other problems, it can achieve the effect of good water absorption and air permeability, high color fastness and bright color
- Summary
- Abstract
- Description
- Claims
- Application Information
AI Technical Summary
Problems solved by technology
Method used
Examples
Embodiment 1
[0024] (1) Configure the surface modifier by weight percentage, mix 10% benzoyl chloride, 3% sodium hydroxide, 2% organic silicon emulsion, 25% diethylene glycol, and 60% tap water to mix evenly;
[0025] (2) configure solubilizing agent by weight percentage, stir and mix 50% glycerin and 50% tap water;
[0026] (3) Pretreatment and transfer printing, etc. The conventionally treated pure cotton fabric is first dipped and rolled twice with a surface modifier, the excess rate is controlled at 80%, dried at 60°C, baked at 170°C for 100 seconds, and then The solubilizer is dipped and rolled, the excess rate is controlled to 80%, and it is dried at 70°C. Finally, it is transferred to the thermal transfer printing machine with disperse yellow SE-3GE at 250°C, 25s, 1.2amt, and corresponding hot water washing , soaping, hot water washing and cold water washing and other washing treatments are sufficient.
Embodiment 2
[0028] (1) configure surface modifier by weight percentage, with benzoyl thioglycolate sodium 25%, sodium carbonate 2.5%, baking soda 1%, anionic softener WML2%, anionic softener stasoft 747 1%, poly Ethylene glycol (molecular weight 400) 15%, distilled water 53.5%, stir and mix evenly;
[0029] (2) configure the solubilizing agent by weight percentage, mix 35% polyethylene glycol (polyethylene glycol) (molecular weight 200) 5%, and distilled water 60% to mix evenly;
[0030] (3) Pretreatment and transfer printing, etc. The conventionally treated pure cotton fabric is first dipped and rolled twice with a surface modifier, the excess rate is controlled at 82%, dried at 63°C, baked at 175°C for 100 seconds, and then The solubilizer is subjected to two-dipping and two-rolling, and the excess rate is controlled to 82%, and it is dried at 70°C. Finally, the disperse yellow SE-3GE is used on the thermal transfer printing machine, and the transfer printing and corresponding hot water...
Embodiment 3
[0032] (1) configure surface modifier by weight percentage, sodium benzoylsalicylate 25%, soda 3%, sodium hydroxide 1%, sodium dihydrogen phosphate 1%, nonionic softener FD-200 2% , glycerol 5%, polyethylene glycol (molecular weight 600) 10%, deionized water 53% stir and mix evenly;
[0033] (2) configure solubilizing agent by weight percentage, polyethylene glycol (molecular weight 200) 25%, deionized water 75% stir and mix evenly;
[0034] (3) Pretreatment and transfer printing, etc. The conventionally treated pure cotton fabric is first three-dipped and three-rolled with a surface modifier, the excess rate is controlled at 83%, dried at 67°C, baked at 180°C for 95 seconds, and then processed. The solubilizer is dipped and rolled, the excess rate is controlled to 83%, and it is dried at 68°C. Finally, it is transferred to the thermal transfer printing machine with Disperse Red E-4B at 250°C, 25s, 1.2amt, and the corresponding hot water washing , soaping, hot water washing a...
PUM
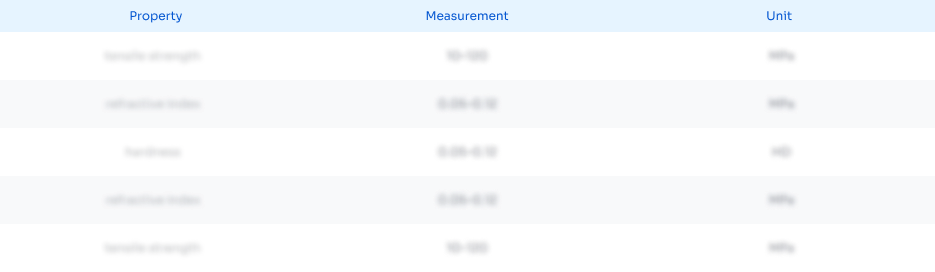
Abstract
Description
Claims
Application Information

- R&D
- Intellectual Property
- Life Sciences
- Materials
- Tech Scout
- Unparalleled Data Quality
- Higher Quality Content
- 60% Fewer Hallucinations
Browse by: Latest US Patents, China's latest patents, Technical Efficacy Thesaurus, Application Domain, Technology Topic, Popular Technical Reports.
© 2025 PatSnap. All rights reserved.Legal|Privacy policy|Modern Slavery Act Transparency Statement|Sitemap|About US| Contact US: help@patsnap.com