Plasma display panel and method for manufacturing same
A plasma and display panel technology, applied in the direction of AC plasma display panels, cold cathode manufacturing, electrode system manufacturing, etc., can solve the problems of insufficient power consumption, difficulty in improving luminous efficiency, high discharge start voltage, etc., and achieve the purpose of suppressing electrostatic capacitance Effects of increasing and reliably starting sustaining discharge and lowering discharge start voltage
- Summary
- Abstract
- Description
- Claims
- Application Information
AI Technical Summary
Problems solved by technology
Method used
Image
Examples
no. 1 Embodiment approach
[0118] FIG. 1(a) is a cross-sectional view of the unit discharge cell of the PDP 101 in the first embodiment of the present invention, which is cut along a plane perpendicular to the partition wall 114. As shown in FIG. Fig. 1(b) is a cross-sectional view taken along the plane indicated by X-Y in Fig. 1(a). In addition, for convenience, only the unit discharge cells of the PDP are shown in FIG. 1, but in the PDP of the first embodiment, a plurality of discharge cells for emitting red, green, and blue lights are arranged in a matrix shape .
[0119] 1. Structure of PDP101
[0120] As shown in Fig. 1(a), the PDP101 is formed by a front panel 102 and a back panel 103 arranged facing each other. In the front panel 102 of the PDP101, a display electrode pair 104 is formed on one main surface of a thin substrate 110, and a dielectric layer 107 and a protective film are sequentially laminated so as to cover the main surface of the substrate 110 on which the display electrode pair 104 is ...
Embodiment 1
[0208] The PDP of Example 1 is the same as the PDP shown in the above-mentioned first embodiment, so its description is omitted.
Embodiment 2
[0210] In the PDP of the second embodiment, the relative permittivity ε of the dielectric layer 107 is set to 2.3, and the thickness d is set to 10 μm, except that it is the same as the PDP of the first embodiment, so the description is omitted.
PUM
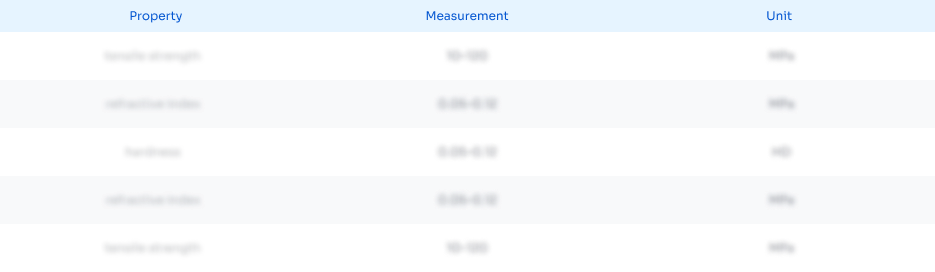
Abstract
Description
Claims
Application Information

- R&D Engineer
- R&D Manager
- IP Professional
- Industry Leading Data Capabilities
- Powerful AI technology
- Patent DNA Extraction
Browse by: Latest US Patents, China's latest patents, Technical Efficacy Thesaurus, Application Domain, Technology Topic, Popular Technical Reports.
© 2024 PatSnap. All rights reserved.Legal|Privacy policy|Modern Slavery Act Transparency Statement|Sitemap|About US| Contact US: help@patsnap.com