Method for manufacturing backboard used for packaging photovoltaic module
A photovoltaic module packaging and manufacturing method technology, applied in the direction of final product manufacturing, sustainable manufacturing/processing, electrical components, etc., can solve the problems of poor process adaptability and waste, achieve high corrosion rate, reduce the pressure of environmental pollution, save energy material effect
- Summary
- Abstract
- Description
- Claims
- Application Information
AI Technical Summary
Problems solved by technology
Method used
Image
Examples
Embodiment 1
[0032] Such as figure 1 As shown, the method for manufacturing a backplane for photovoltaic module encapsulation in this embodiment includes the following steps: first, compound the thin metal layer 5 and the backplane substrate 14 to form a backplane 1, and the backplane substrate 14 is an insulating material for supporting The thin metal layer 5 is metal aluminum foil. The metal sheet can also consist of two or more layers of different metals, such as aluminum and zinc. The metal thin layer can also be coated with another or several metals on the surface of one layer of metal, such as a layer of zinc and copper coated on the surface of aluminum. The thin metal layer can also be an aluminum alloy.
[0033] Next, forming a connecting circuit on the thin metal layer 5 by etching, specifically includes the following steps: placing the back plate 1 flat on the platform 3 in the corrosion tank 2 with the electrolytic etching solution 6, with the thin metal layer 5 facing upward,...
Embodiment 2
[0036] Such as figure 2 As shown, the method for manufacturing a backplane for photovoltaic module encapsulation in this embodiment includes the following steps: first, compound the thin metal layer 5 with the backplane substrate 14, open an opening at an appropriate position of the backplane substrate 14, and allow the thin metal layer to pass through The opening communicates with the positive pole of the power supply. The metal thin layer 5 is metal aluminum foil. The metal sheet can also consist of two or more layers of different metals, such as aluminum and zinc. The metal thin layer can also be coated with another or several metals on the surface of one layer of metal, such as a layer of zinc and copper coated on the surface of aluminum. The thin metal layer can also be an aluminum alloy.
[0037] Secondly, forming a connecting circuit on the thin metal layer 5 by etching, specifically includes the following steps: placing the backplane substrate 14 compounded with th...
PUM
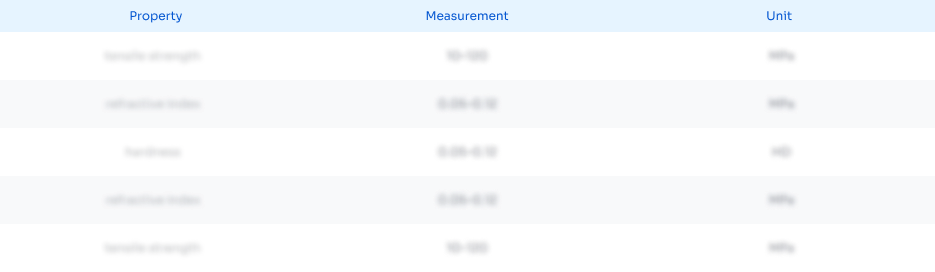
Abstract
Description
Claims
Application Information

- R&D
- Intellectual Property
- Life Sciences
- Materials
- Tech Scout
- Unparalleled Data Quality
- Higher Quality Content
- 60% Fewer Hallucinations
Browse by: Latest US Patents, China's latest patents, Technical Efficacy Thesaurus, Application Domain, Technology Topic, Popular Technical Reports.
© 2025 PatSnap. All rights reserved.Legal|Privacy policy|Modern Slavery Act Transparency Statement|Sitemap|About US| Contact US: help@patsnap.com