Fired-coal furnace and its additive
A kiln and coal-burning technology, used in furnaces, fuels, combustion chambers, etc., can solve the problems of insufficient combustion of coal and large heat loss, and achieve the effect of significant coal saving, fast burning speed and high calorific value.
- Summary
- Abstract
- Description
- Claims
- Application Information
AI Technical Summary
Problems solved by technology
Method used
Image
Examples
Embodiment
[0026] Constructing a horizontal ceramic tile sintering kiln with the technical scheme of the invention
[0027] The outer side of the furnace body 1 is wrapped with an insulating layer, the inner side of the furnace body is coated with an inherent far-infrared reflective layer 3, a grate 4 is installed in the lower part of the furnace cavity, and a coal-fired layer 5 is formed on the upper part of the grate. An air supply and slag discharge cavity 6 is formed between the side and the inner cavity of the furnace, and a combustion heating cavity 7 is formed on the upper part of the coal combustion layer of the furnace body, and ceramic tiles are sintered in the combustion heating cavity.
[0028] Insulation layer composition: Take aluminum silicate rock wool 10, sepiolite 50, polyvinyl alcohol 1, rare earth composite adhesive 0.8, sodium bentonite 10 and OP10 penetrant 1 part and closed-cell hollow ceramic powder 30% by weight. 70% mixture of closed-cell porous ceramic particles 0....
PUM
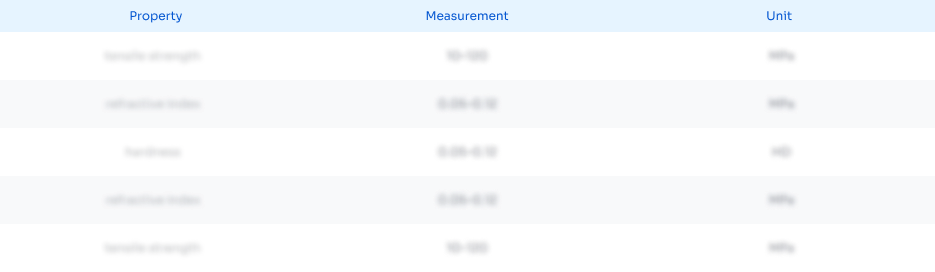
Abstract
Description
Claims
Application Information

- R&D
- Intellectual Property
- Life Sciences
- Materials
- Tech Scout
- Unparalleled Data Quality
- Higher Quality Content
- 60% Fewer Hallucinations
Browse by: Latest US Patents, China's latest patents, Technical Efficacy Thesaurus, Application Domain, Technology Topic, Popular Technical Reports.
© 2025 PatSnap. All rights reserved.Legal|Privacy policy|Modern Slavery Act Transparency Statement|Sitemap|About US| Contact US: help@patsnap.com