Process of producing nanometer level soybean protein powder
A technology of soybean protein powder and production method, which is applied in the direction of protein food ingredients, protein composition of vegetable seeds, food forming, etc., can solve the problems of low biological value, large particle size distribution, low nutritional value, etc., and achieve simple production process , easy to digest and absorb, high nutritional value
- Summary
- Abstract
- Description
- Claims
- Application Information
AI Technical Summary
Problems solved by technology
Method used
Examples
Embodiment 1
[0014] Embodiment one takes soybean protein isolate powder as raw material, and its processing steps are:
[0015] 1. Material pretreatment stage: (1) Colloid mill one-step pretreatment: configure 5% soybean protein isolate solution, pass through the colloid mill to pretreat the soybean protein isolate solution, so that the soybean protein isolate is evenly mixed in the aqueous solution; (2) Low-pressure two-step pretreatment: Homogenize the one-step pretreated material through a low-pressure homogenizer, the treatment pressure is ≤20MPa, and the treatment times are ≤3 times.
[0016] 2. The heat treatment stage of the material: heat the pretreated material in a water bath for ≤30 minutes at a temperature of 35°C.
[0017] 3. Ultra-high pressure homogenization treatment stage of materials: After heat treatment, keep the temperature constant, and perform high-pressure homogenization through a dynamic ultra-high pressure homogenizer. 5 times.
[0018] 4. Subsequent processing ...
Embodiment 2
[0021] Embodiment two takes soybean protein isolate powder as raw material, and its processing step is:
[0022] 7. Material pretreatment stage: (1) Colloid mill one-step pretreatment: configure 10% soybean protein isolate, and pretreat the soybean protein isolate solution through the colloid mill, so that the soybean protein isolate is evenly mixed in the aqueous solution; (2) Low pressure Two-step pretreatment: Homogenize the one-step pretreated material through a low-pressure homogenizer, the treatment pressure is ≤20MPa, and the treatment times are ≤3 times.
[0023] 8. The heat treatment stage of the material: heat the pretreated material in a water bath for ≤30 minutes at a temperature of 50°C.
[0024] 9. Ultra-high pressure homogenization treatment stage of materials: After heat treatment, keep the temperature constant, and perform high-pressure homogenization through a dynamic ultra-high pressure homogenizer. 5 times.
[0025] 10. Subsequent processing stage: use a ...
PUM
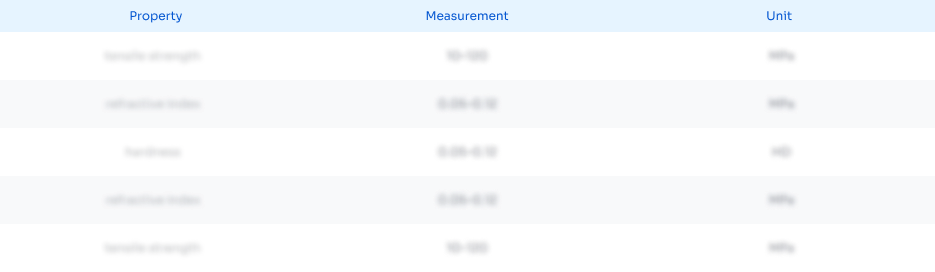
Abstract
Description
Claims
Application Information

- R&D
- Intellectual Property
- Life Sciences
- Materials
- Tech Scout
- Unparalleled Data Quality
- Higher Quality Content
- 60% Fewer Hallucinations
Browse by: Latest US Patents, China's latest patents, Technical Efficacy Thesaurus, Application Domain, Technology Topic, Popular Technical Reports.
© 2025 PatSnap. All rights reserved.Legal|Privacy policy|Modern Slavery Act Transparency Statement|Sitemap|About US| Contact US: help@patsnap.com