Urea formaldehyde resin, and preparation method
A technology of urea-formaldehyde resin and formaldehyde, which is applied in the field of urea-formaldehyde resin for the production of wood-based panels and its preparation, can solve the problems of physical and mechanical properties, durability and water resistance of wood-based panels, the increase of free formaldehyde in wood-based panels, and the decrease of water-solubility of urea-formaldehyde resin, etc. problems, achieve the effects of shortening the production cycle, improving physical and mechanical properties, and improving curing performance
- Summary
- Abstract
- Description
- Claims
- Application Information
AI Technical Summary
Problems solved by technology
Method used
Examples
Embodiment 1
[0024] Raw material formula:
[0025] raw material
Weight (kg)
Content (%)
Remark
formaldehyde
200
45
urea
156
98
U1=25
[0026] U2=65
U3=40
U4=26
1
Type 1799
0.4
100
Herotropine
1
98
Appropriate amount
20
Adjust pH value
Appropriate amount
30
Adjust pH value
[0027] Note: The molar ratio of formaldehyde to urea is 1.18.
[0028] Concrete reaction steps include:
[0029] 1) Add formaldehyde and polyvinyl alcohol into the reaction kettle, then add maleic anhydride, stir evenly and check the pH value, pH=2.0-2.5;
[0030] 2) Add urea for the first time, heat up to a temperature of 50±2°C within 15 minutes, keep warm and react until the fog point appears in 30°C water (that is, drop the reaction solution into a beaker filled with 30°C...
experiment example 1
[0066] The urea-formaldehyde resin produced by the method of embodiment one and the method of comparative example one is used to prepare 16mm and 18mm particle boards respectively, and the processes shown in the following table 1 are all executed during production:
[0067] Process parameters
16mm particle board
18mm particle board
Surface, core layer
the surface
core layer
the surface
core layer
Raw rubber (kg)
100
100
100
100
Emulsion (kg)
8.9
10.5
8.9
10.5
water (kg)
20
0
20
0
Sizing ratio (%)
18.1
12.6
18.1
12.6
Hardener(%)
0
1.5
0
1.5
Hot pressing temperature (℃)
195~210
Hot pressing time (min)
2.7
3.0
Nominal thickness (mm)
16
18
Average amount of glue (kg / m 3 )...
Embodiment 2
[0074] Raw material formula:
[0075] raw material
Weight (kg)
Content (%)
Remark
formaldehyde
200
50
urea
173
98
U1=30
U2=75
U3=45
U4=23
5
Type 1799
0.4
100
Herotropine
3
98
Appropriate amount
20
Adjust pH value
Appropriate amount
30
Adjust pH value
[0076] Note: The molar ratio of formaldehyde to urea is 1.18
[0077] Concrete reaction step is with embodiment one
[0078] Resin quality index:
[0079] Solid content 64-66%
[0080] pH 7.5-8.0
[0081] Viscosity (20°C) 33-40 (S, Tu-4 cups)
[0082] Curing speed 45-60 seconds
[0083] Free formaldehyde content <0.2%
[0084] Water solubility ≥1.0
[0085] Storage period ≥15 days
[0086] Resin reaction time and cost:
[0087] Resin reaction time: 6 hours; resin cost: 18...
PUM
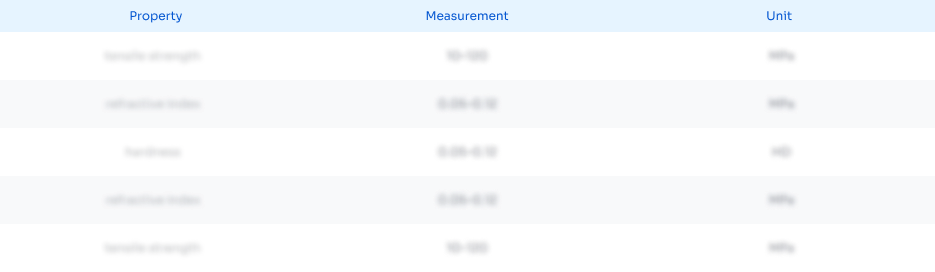
Abstract
Description
Claims
Application Information

- Generate Ideas
- Intellectual Property
- Life Sciences
- Materials
- Tech Scout
- Unparalleled Data Quality
- Higher Quality Content
- 60% Fewer Hallucinations
Browse by: Latest US Patents, China's latest patents, Technical Efficacy Thesaurus, Application Domain, Technology Topic, Popular Technical Reports.
© 2025 PatSnap. All rights reserved.Legal|Privacy policy|Modern Slavery Act Transparency Statement|Sitemap|About US| Contact US: help@patsnap.com