Manufacture method of super-hard grinding tool containing metallic or ceramic binder
A technology of vitrified bond and manufacturing method, which is applied in the direction of manufacturing tools, metal processing equipment, grinding devices, etc., can solve the problems of uneven carcass density, low labor productivity, poor stability of mold precision, etc., and achieve uniform carcass density Consistent, the realization of production automation, the effect of improving the internal quality
- Summary
- Abstract
- Description
- Claims
- Application Information
AI Technical Summary
Problems solved by technology
Method used
Image
Examples
Embodiment 1
[0054] Diamond is selected as the superabrasive, and the composition of the metal powder is (percentage by weight): 20% copper, 70% iron, 5% tin, 3% cobalt, and 2% graphite. Mix the above-mentioned working layer powder raw materials evenly. Assemble the mold and apply a release agent inside it, fill the mold with matrix powder and working layer powder raw materials in sequence according to the process, add the pressure head, move to the press to pressurize quickly, and the pressure is controlled at 350 MPa , hold the pressure for 2 minutes; remove the mold from the press, and get the green mold after demoulding; use the method of first combining and then heating and then pressing to combine the green mold with the pyrophyllite as the medium to form a green mold -Medium combination, so that pyrophyllite is evenly distributed around the green body, move the green body-medium combination into a heating furnace, heat it to 850°C and keep it warm for 3 hours; move the heated green ...
Embodiment 2
[0056] Cubic boron nitride is selected as the superhard abrasive material, and the composition of the metal powder is (percentage by weight): 50% bronze, 45% iron, 3% tungsten, and 2% graphite. Mix cubic boron nitride and metal powder of a certain particle size evenly in proportion to obtain the powder material of the working layer, assemble the mold and apply the release agent, and put the matrix powder and the powder material of the working layer in the bag in sequence. The sheath is sealed after vacuum to obtain a green body. The green body and pyrophyllite are combined to form a green body-medium combination, so that the pyrophyllite is evenly distributed around the green body, the green body-medium combination is moved into a heating furnace, heated to 860 ° C and kept for 3 hours, and the green body-medium combination Move the body into the pot-shaped mold, add the pressure head, pressurize quickly on the press, the pressure is 500 MPa, hold the pressure for 20 minutes, ...
Embodiment 3
[0058] Diamond is selected as the superabrasive, and the composition of the metal powder is (percentage by weight): 18% tungsten carbide, 5% nickel, 4% manganese, 3% cobalt, and 70% copper. The medium is made of amorphous non-metallic material, and its composition is (percentage by weight): 5% B 2 o 3 , 15% sodium oxide and 80% silicon oxide, cold pressing pressure is 500 MPa, holding pressure for 1 hour, hot pressing pressure is 200 MPa, holding pressure for 25 minutes, heating temperature is 800 ° C, holding time is 2 hours , all the other are identical with embodiment 1.
PUM
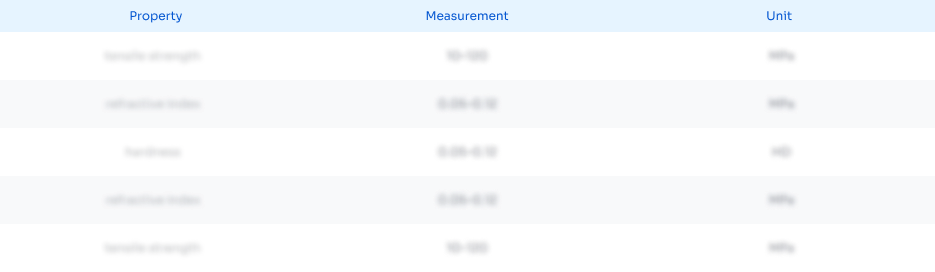
Abstract
Description
Claims
Application Information

- R&D
- Intellectual Property
- Life Sciences
- Materials
- Tech Scout
- Unparalleled Data Quality
- Higher Quality Content
- 60% Fewer Hallucinations
Browse by: Latest US Patents, China's latest patents, Technical Efficacy Thesaurus, Application Domain, Technology Topic, Popular Technical Reports.
© 2025 PatSnap. All rights reserved.Legal|Privacy policy|Modern Slavery Act Transparency Statement|Sitemap|About US| Contact US: help@patsnap.com