Air cold plate sealing forming technology of aluminum alloy
A molding process, aluminum alloy technology, applied in metal processing equipment, manufacturing tools, edge parts of workpieces, etc., can solve the problems of low production efficiency, low joint strength, poor compactness of brazing seams, etc., to improve the ability to withstand deep processing, Improve the welding yield and ensure the effect of sealing requirements
- Summary
- Abstract
- Description
- Claims
- Application Information
AI Technical Summary
Problems solved by technology
Method used
Image
Examples
Embodiment 1
[0020] Embodiment 1: Aluminum alloy air-cooled cold plate
[0021] Dimensions of cold plate: 367mm×183mm×22mm
[0022] Processing steps
[0023] 1. CNC machining cold plate shell:
[0024] Clamping blank aluminum plate 373mm×216mm×25mm
[0025] 1. According to the structural design, the rough shape of the cold plate shell is processed 367mm×183mm×22mm, and six sides are milled, and the size is 367mm×183mm×22mm.
[0026] 2. Mill 247 in the center of the cold plate shell -0.15 -0.05 ×140 -0.15 -0.05 ×13mm square cavity, and then mill a 4mm wide step around it to ensure that the upper slot is 255, + 0.05 +05 ×148+ 0.05 + 015 ×4mm,
[0027] 3. Three brazing process holes of Φ2-3mm are opened at both ends of the cold plate shell;
[0028] 2. CNC machining cover plate:
[0029] Clamping blank aluminum plate 263mm×156mm×4mm
[0030] 1. Milling four sides, for size 255 -0.15 -0.05 ×148 -0.15 -0.05 ,
[0031] 2. Deburring, repairing four corners R3;
[0032] 3. Radi...
Embodiment 2
[0045] Embodiment 2: Aluminum alloy air-cooled cold plate
[0046] Dimensions of cold plate: 367mm×183mm×22mm
[0047] Processing steps
[0048] 1. CNC machining cold plate shell:
[0049] Clamping blank aluminum plate 373mm×216mm×25mm
[0050] 1. According to the structural design, the rough shape of the cold plate shell is processed 367mm×183mm×22mm, and the six sides are milled. The size is 367mm×183mm×22mm,
[0051] 2. Mill 247 in the center of the cold plate shell -0.15 -0.05 ×140 -0.15 -0.05 ×13mm square cavity, and then milling 4mm wide steps around to ensure that the upper groove is 255+ 0.05 +015 ×148+ 0.05 +005 ×4mm,
[0052] 3. Three brazing process holes of Φ2-3mm are opened at both ends of the cold plate shell;
[0053] 2. CNC machining cover plate:
[0054] Clamping blank aluminum plate 263mm×156mm×4mm
[0055] 1. Milling four sides, for size 255 -0.15 -0.05 ×148 -0.15 -0.05 ,
[0056] 2. Deburring, repairing four corners R3;
[0057] 3. Radia...
PUM
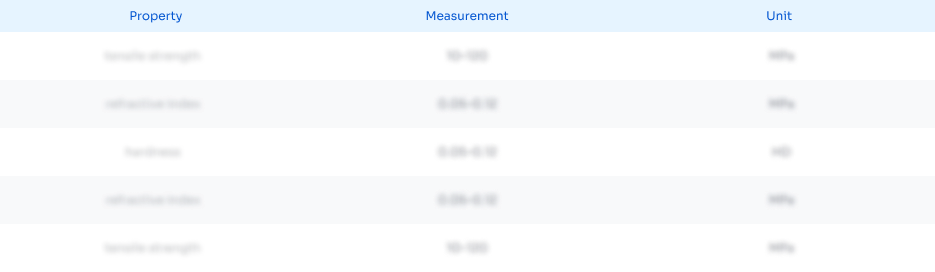
Abstract
Description
Claims
Application Information

- R&D
- Intellectual Property
- Life Sciences
- Materials
- Tech Scout
- Unparalleled Data Quality
- Higher Quality Content
- 60% Fewer Hallucinations
Browse by: Latest US Patents, China's latest patents, Technical Efficacy Thesaurus, Application Domain, Technology Topic, Popular Technical Reports.
© 2025 PatSnap. All rights reserved.Legal|Privacy policy|Modern Slavery Act Transparency Statement|Sitemap|About US| Contact US: help@patsnap.com