Wearable iron-based TiC-ceramic-containing powder cored wire for electric arc spraying
A kind of arc spraying, powder core wire technology, applied in the direction of coating, fusion spraying, metal material coating technology, etc. effect of the problem
- Summary
- Abstract
- Description
- Claims
- Application Information
AI Technical Summary
Problems solved by technology
Method used
Examples
Embodiment 1
[0019] A stainless steel strip (304) of 10×0.4 (10 mm in width and 0.4 mm in thickness) is selected. Roll it into a U shape first. Get 0.200 kilogram of ferroboron powder, 0.040 kilogram of metallic nickel powder, 0.045 kilogram of metallic chromium powder, 0.015 kilogram of metallic titanium powder, 0.100 kilogram of iron powder (the particle size of powder is to pass through 40 mesh sieves), 0.100 kilogram of titanium carbide ceramic powder, particle size is 60 mesh. The various powders taken are put into the powder mixer and mixed for 10 minutes, and then the mixed powder is added into a U-shaped stainless steel belt groove, and the filling rate is 25%. Close the U-shaped groove so that the powder is wrapped in it. Then make it pass through the drawing dies with diameters of: 3.0mm, 2.8mm, 2.6mm, 2.5mm, 2.4mm, 2.3mm, 2.2mm, 2.1mm, 2.0mm, 1.9mm, 1.8mm, 1.7mm, 1.6mm, Drawing and reducing the diameter step by step, and finally make the diameter reach 1.6mm. Spray metal coa...
Embodiment 2
[0021] A stainless steel strip (304) of 10×0.3 (10 mm in width and 0.3 mm in thickness) is selected. Roll it into a U shape first. Get 0.175 kilogram of ferroboron powder, 0.010 kilogram of metallic nickel powder, 0.050 kilogram of metallic chromium powder, 0.010 kilogram of metallic titanium powder, 0.105 kilogram of iron powder (the particle size of powder is to pass through 40 mesh sieves), 0.150 kilogram of titanium carbide ceramic powder, particle size is 60 mesh. The various powders taken were put into a powder mixer and mixed for 10 minutes, and then the mixed powder was added into a U-shaped stainless steel belt groove, and the filling rate was 32%. Close the U-shaped groove so that the powder is wrapped in it. Then make it pass through drawing dies with diameters of 3.0mm, 2.8mm, 2.6mm, 2.5mm, 2.4mm, 2.3mm, 2.2mm, 2.1mm, 2.0mm, 1.9mm, 1.8mm, and draw and reduce diameter, and finally make it 1.8mm in diameter. Spray metal coating on the surface of equipment and pip...
Embodiment 3
[0023] A stainless steel strip (304) of 14×0.3 (14 mm in width and 0.3 mm in thickness) is selected for use. Roll it into a U shape first. Get 0.150 kilogram of ferroboron powder, 0.050 kilogram of metallic nickel powder, 0.025 kilogram of metallic chromium powder, 0.015 kilogram of metallic titanium powder, 0.100 kilogram of iron powder (the particle size of powder is to pass through 40 mesh sieves), 0.160 kilogram of titanium carbide ceramic powder, particle size is 60 mesh. The various powders taken were put into a powder mixer and mixed for 10 minutes, and then the mixed powder was added into a U-shaped stainless steel belt groove, and the filling rate was 35%. Close the U-shaped groove so that the powder is wrapped in it. Then make it pass through drawing dies with diameters of 3.0mm, 2.8mm, 2.6mm, 2.5mm, 2.4mm, 2.3mm, 2.2mm, 2.1mm, 2.0mm, draw and reduce the diameter one by one, and finally make the diameter up to 2.0mm. Spray metal coating on the surface of equipmen...
PUM
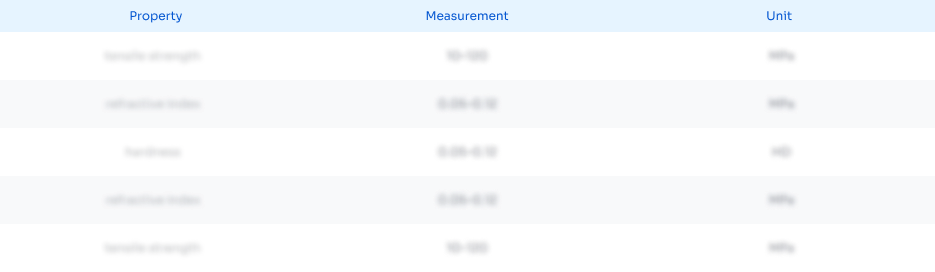
Abstract
Description
Claims
Application Information

- R&D Engineer
- R&D Manager
- IP Professional
- Industry Leading Data Capabilities
- Powerful AI technology
- Patent DNA Extraction
Browse by: Latest US Patents, China's latest patents, Technical Efficacy Thesaurus, Application Domain, Technology Topic, Popular Technical Reports.
© 2024 PatSnap. All rights reserved.Legal|Privacy policy|Modern Slavery Act Transparency Statement|Sitemap|About US| Contact US: help@patsnap.com