Contact line of bronze in use for electrified railroad in high speed, and preparation method
A technology of electrified railways and copper-tin alloys, applied in the direction of cable/conductor manufacturing, other manufacturing equipment/tools, electrical components, etc., can solve problems such as low strength, high temperature resistance, poor corrosion resistance and wear resistance, and achieve uniform composition , Improve the strength, reduce the effect of gas content
- Summary
- Abstract
- Description
- Claims
- Application Information
AI Technical Summary
Problems solved by technology
Method used
Image
Examples
Embodiment 1
[0023] Each component is prepared according to the following weight:
[0024] Tin 5000×0.16%×(1+3%)=8.24kg
[0025] Zirconium 5000×0.008%×(1+30%)=0.52kg
[0026] Mixed rare earth 5000×0.01%×(1+20%)=0.6kg
[0027] Copper 5000×(100-0.16-0.007-0.01-0.008-0.01)%=4991.1kg
[0028] Melt 5% of the copper weight in the raw material, that is, 249.6kg, 8.24kg tin, and 0.52kg zirconium into an alloy matrix in a vacuum induction melting furnace, and divide it into 250 equal parts, and each part is mixed with 0.0024kg mixed rare earth and 18.9kg copper. Add it to a power frequency induction furnace with a sealing device, and draw it up according to the above melting and drawing process 15.8mm cast stem. The total weight of the obtained casting rod is 5 tons, and the content of each element is: 0.16% of tin, 0.008% of zirconium, 0.01% of mixed rare earth, and the balance of copper. The cast rod is heated to 300°C in an argon-protected induction furnace and then extruded by a continuou...
Embodiment 2
[0030] Each component is prepared according to the following weight:
[0031] Tin 5000×0.2%×(1+3%)=10.3kg
[0032] Zirconium 5000×0.01%×(1+30%)=0.65kg
[0033] Magnesium 5000×0.009%×(1+20%)=0.54kg
[0034] Mixed rare earth 5000×0.016%×(1+20%)=0.96kg
[0035] Silver 5000×0.01%=0.5kg
[0036] Copper 5000×(100-0.2-0.009-0.01-0.016-0.01)%=4987.8kg
[0037] Melt 8% of the copper weight in the raw material, that is, 399kg with 10.3kg tin, 0.65kg zirconium, 0.54kg magnesium, and 0.5kg silver into an alloy matrix in a vacuum induction melting furnace, and divide it into 400 equal parts, each part with 0.0024kg Add the mixed rare earth and 11.47kg copper into the power frequency induction furnace with a sealing device, and follow the above-mentioned smelting and upward induction process. 16.0mm cast rod. The total weight of the cast rod obtained is 5 tons, and the content of each element is: 0.20% tin, 0.009% magnesium, 0.01% zirconium, 0.016% mixed rare earth, 0.01% silver, and...
Embodiment 3
[0039] Each component is prepared according to the following weight:
[0040] Tin 6000×0.3%×(1+3%)=18.54kg
[0041] Zirconium 6000×0.01%×(1+30%)=0.78kg
[0042] Magnesium 6000×0.007%×(1+20%)=0.504kg
[0043] Mixed rare earth 6000×0.02%×(1+20%)=1.44kg
[0044] Silver 6000×0.007%=0.42kg
[0045] Copper 6000×(100-0.3-0.007-0.01-0.02-0.007)%=5979.36kg
[0046] Melt 10% of the copper weight in the raw material, that is, 598kg with 18.54kg tin, 0.78kg zirconium, 0.504kg magnesium, and 0.42kg silver into an alloy matrix in a vacuum induction melting furnace, and divide it into 600 equal parts, each with 0.0024kg Add the mixed rare earth and 9kg copper into the power frequency induction furnace with a sealing device, and follow the above-mentioned smelting and upward induction process. 17.0mm cast stem. The total weight of the obtained casting rod is 6 tons, and the content of each element is: 0.3% of tin, 0.007% of magnesium, 0.01% of zirconium, 0.02% of mixed rare earth, 0.007...
PUM
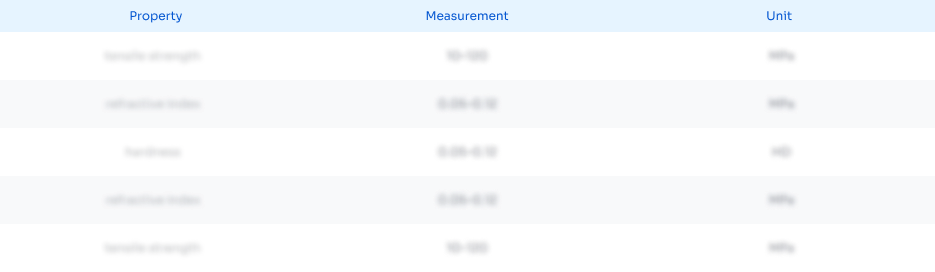
Abstract
Description
Claims
Application Information

- R&D
- Intellectual Property
- Life Sciences
- Materials
- Tech Scout
- Unparalleled Data Quality
- Higher Quality Content
- 60% Fewer Hallucinations
Browse by: Latest US Patents, China's latest patents, Technical Efficacy Thesaurus, Application Domain, Technology Topic, Popular Technical Reports.
© 2025 PatSnap. All rights reserved.Legal|Privacy policy|Modern Slavery Act Transparency Statement|Sitemap|About US| Contact US: help@patsnap.com