Semiconductor silicon material water base cutting liquid
A silicon material and cutting fluid technology, applied in the field of high-efficiency alkaline semiconductor silicon material water-based cutting fluid, can solve problems affecting VLSI, waste materials, increase processing volume, etc., to facilitate cleaning and subsequent processing, avoid Chemical bonding adsorption, the effect of solving stress problems
- Summary
- Abstract
- Description
- Claims
- Application Information
AI Technical Summary
Problems solved by technology
Method used
Examples
Embodiment 1
[0022] Example 1: Prepare 1000 g of cutting fluid at a production concentration. The polyethylene glycol in this example has a low molecular weight, and the resulting cutting fluid is suitable for cutting semiconductor materials.
[0023] Take 900g of polyethylene glycol (PEG200), 90g of amine base --- hydroxyethylethylenediamine, 10g of chelating agent-FA / O, and the balance is deionized water.
[0024] In the polyethylene glycol (PEG200) under continuous stirring, add the above-mentioned amount of hydroxyethylethylenediamine and chelating agent FA / O slowly and sequentially, and stir until uniform to obtain 1000g of cutting fluid with a production concentration. When used in production, it is used with deionized water at a weight percentage of 1:20.
Embodiment 2
[0025] Embodiment 2: Prepare 1000g cutting fluid
[0026] Take 500g of polyethylene glycol (PEG600) in paste form, 300g of amine base-triethanolamine, 100g of chelating agent-FA / O, and the balance is deionized water.
[0027] At a temperature of 40-60°C, under continuous stirring, dissolve the paste-like polyethylene glycol (PEG600) in deionized water, and slowly add the above-mentioned amount of triethanolamine and chelating agent FA / O in sequence under continuous stirring, Stir until uniform to obtain 1000g cutting fluid.
[0028] The polyethylene glycol in this embodiment is still low molecular weight, and the resulting cutting fluid is suitable for cutting semiconductor materials. When used in production, it is used with deionized water at a weight percentage of 1:15.
Embodiment 3
[0029] Embodiment 3: Prepare 1000g cutting fluid
[0030] Take 300g of solid polyethylene glycol (PEG1000), 200g of amine base-triethanolamine, 50g of chelating agent-FA / O, and the balance is deionized water.
[0031] Dissolve solid polyethylene glycol (PEG1000) in deionized water, slowly add the above-mentioned amount of triethanolamine and chelating agent FA / O under continuous stirring, and stir until uniform to obtain 1000g of cutting fluid.
[0032] The polyethylene glycol in this embodiment has a high molecular weight, and the resulting cutting fluid is not only suitable for cutting semiconductor materials, but also suitable for cutting high-hardness materials, such as diamonds. When used in production, it is used with deionized water at a weight percentage of 1:10.
PUM
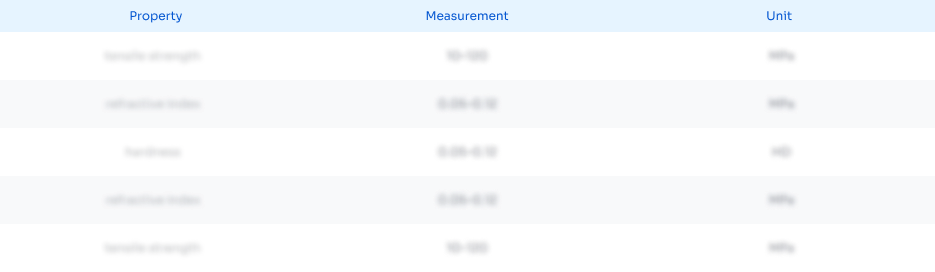
Abstract
Description
Claims
Application Information

- R&D
- Intellectual Property
- Life Sciences
- Materials
- Tech Scout
- Unparalleled Data Quality
- Higher Quality Content
- 60% Fewer Hallucinations
Browse by: Latest US Patents, China's latest patents, Technical Efficacy Thesaurus, Application Domain, Technology Topic, Popular Technical Reports.
© 2025 PatSnap. All rights reserved.Legal|Privacy policy|Modern Slavery Act Transparency Statement|Sitemap|About US| Contact US: help@patsnap.com