Method for treating heavy oil
- Summary
- Abstract
- Description
- Claims
- Application Information
AI Technical Summary
Benefits of technology
Problems solved by technology
Method used
Image
Examples
example 1
[0059]Upgrading Oil from a Texas Oil Source
[0060]The oil came from a heavy oil field located in Southwestern Texas. Fifty grams of the Southwestern Texas HCO was blended with 175 grams of iso-octane solvent (225 grams total) for sonic deasphalting in a baffled 1.7 litre stainless steel reaction chamber. The deasphalting occurred at 25 kW power applied continuously for 120 seconds in batch mode in a 1.7 lire sonic reaction chamber. Subsequently the deasphalted material was separated through direct vacuum filtration. Optionally, the subsequent deasphalted oil was oxidized via the prior art described by Boakye (Canadian patent #2,549,358) utilizing acetic acid, hydrogen peroxide, peroxidase enzyme source (i.e. soyabean husk) and iron oxide. The oxidation reaction was quenched through absorption of generated polar compounds and sulfur compounds by passing the deasphalted HCO / solvent / reagent reaction product through a natural clay and activated carbon mixture that removes excess and / or u...
example 2
[0063]Upgrading Oil from a Canadian Oil Source
[0064]Oil from a heavy oil field located near Lloydminster, Alberta, Canada was tested.
[0065]Fifty grams of Lloydminster HCO was blended with 175 grams of iso-octane solvent (225 grams total) for sonic deasphalting in a baffled 1.7 litre stainless steel reaction chamber. The deasphalting occurred at 25 kW power applied continuously for 120 seconds in batch mode. After the deasphalted material was separated through direct vacuum filtration, the subsequent deasphalted oil was oxidized via the prior art described by Boakye (Canadian patent #2,549,358) utilizing acetic acid, hydrogen peroxide, peroxidase enzyme source (i.e. soyabean husk) and iron oxide. The oxidation reaction was quenched through absorption of generated polar compounds and sulfur compounds by passing the deasphalted HCO / solvent / reagent reaction product through a natural clay and activated carbon mixture.
TABLE 4Sample Candidate Oil Balance (Run 081017E-1):InputsMass (kg)Outp...
example 3
[0067]Upgrading Oil from an Albanian Oil Source
[0068]The oil from a heavy oil field located in Albania was tested next.
[0069]Fifty grams of Albanian HCO was blended with 175 grams of iso-octane solvent (225 grams total) for sonic deasphalting in a baffled 1.7 litre stainless steel reaction chamber. The deasphalting occurred at 25 kW power applied continuously for 120 seconds in batch mode. After the deasphalted material was separated through direct vacuum filtration, the subsequent deasphalted oil was oxidized through the prior art described by Boakye (Canadian patent #2,549,358) utilizing acetic acid, hydrogen peroxide, peroxidase enzyme source (i.e. soyabean husk) and iron oxide. The oxidation reaction was quenched through absorption of generated polar compounds and sulfur compounds by passing the deasphalted HCO / solvent / reagent reaction product through a natural clay and activated carbon mixture that remove all excess and / or unconsumed oxidation reagents.
TABLE 6Sample Candidate O...
PUM
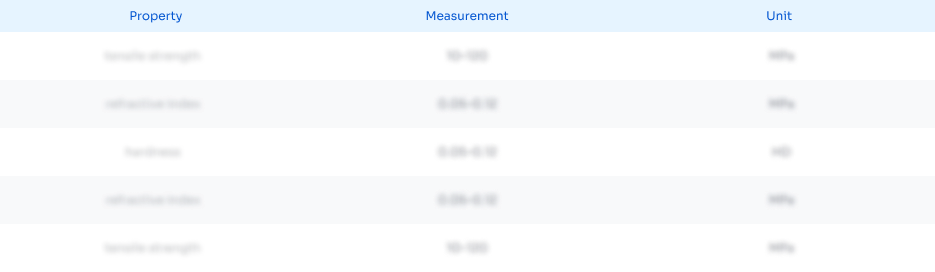
Abstract
Description
Claims
Application Information

- R&D
- Intellectual Property
- Life Sciences
- Materials
- Tech Scout
- Unparalleled Data Quality
- Higher Quality Content
- 60% Fewer Hallucinations
Browse by: Latest US Patents, China's latest patents, Technical Efficacy Thesaurus, Application Domain, Technology Topic, Popular Technical Reports.
© 2025 PatSnap. All rights reserved.Legal|Privacy policy|Modern Slavery Act Transparency Statement|Sitemap|About US| Contact US: help@patsnap.com