Process for improving operation of large-scale combustors
a technology of large-scale combustors and heat exchangers, which is applied in the direction of solid fuel combustion, combustion types, coals, etc., can solve the problems of increasing the stack, reducing the efficiency of combustion of carbonaceous fuels, so as to improve efficiency and reduce stack. , the effect of saving money
- Summary
- Abstract
- Description
- Claims
- Application Information
AI Technical Summary
Benefits of technology
Problems solved by technology
Method used
Image
Examples
example 1
[0039] In this example, magnesium hydroxide was fed to the fuel oil for a residual oil fired electric power plant boiler at a rate of 0.20 kg per 1000 kg. Magnesium hydroxide was also directed into the boiler at positions determined by computational fluid dynamic modeling as described in U.S. Pat. No. 5,894,806, at a rate of 0.20 kg per 1000 kg. In addition, a calcium nitrate combustion catalyst was added to the fuel oil at a rate of 0.25 kg per 1000 kg. The magnesium hydroxide fed the fuel oil performed two roles: it protected the lower furnace against slagging and hot-side corrosion by the mechanism of tying up vanadium in the oil. The magnesium hydroxide also prevented fouling caused by the catalyst from affecting lower furnace cleanliness. Most catalysts used for fossil fuels can also cause fouling in the lower furnace. Data showed base line opacities of 25% opacity and excess O2 levels of 1.5%-2.0%. When the invention was introduced after a CFD model was run, opacity dropped to...
example 2
[0040] A similar set as in Example 1 is run with similar treatment to reduce opacities from 30% to 7%. In this case, the combustion catalyst is fed at a rate of 0.25 kg per 1000 kg of fuel, and the in-furnace injection chemical is Mg, which is fed at a rate of 0.35 kg per 1000 kg of fuel.
example 3
[0041] In this example, an injection of Mg(OH)2 slurry containing copper combustion catalyst increased MW generation while controlling furnace exit gas temperature (FEGT) and steam temperature. The power generation of 150 MW coal fired utility boiler was limited to about 140 MW due to high FEGT and main steam temperature. To overcome this limitation, a chemical treatment mixture of Mg and Cu compositions (comprised of magnesium hydroxide and copper carbonate, with 19% magnesium and 6% copper based on the weight of the slurry) was injected through the lowest elevation Targeted In-Furnace Injection ports. These and other targeted in-furnace injection ports were previously determined through a CFD modeling study.
[0042] With the initial start of Catalyst feed, the gross MW generation increased from increased coal flow rates. The main steam temperature and FEGT stayed within the maximum allowed limit throughout the test. This test was repeated on the following day with a similar result....
PUM
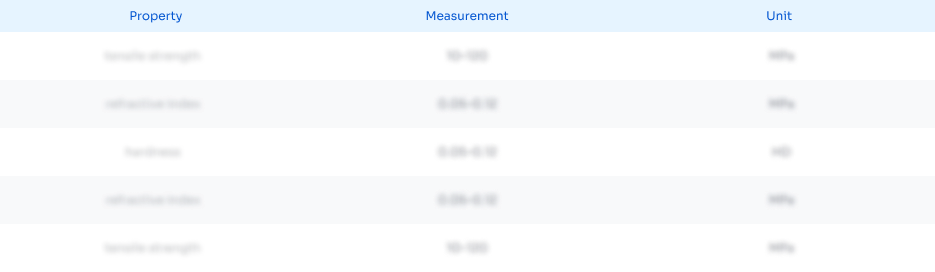
Abstract
Description
Claims
Application Information

- R&D
- Intellectual Property
- Life Sciences
- Materials
- Tech Scout
- Unparalleled Data Quality
- Higher Quality Content
- 60% Fewer Hallucinations
Browse by: Latest US Patents, China's latest patents, Technical Efficacy Thesaurus, Application Domain, Technology Topic, Popular Technical Reports.
© 2025 PatSnap. All rights reserved.Legal|Privacy policy|Modern Slavery Act Transparency Statement|Sitemap|About US| Contact US: help@patsnap.com