Mold for fabricating barrier rib and method of fabricating two-layered barrier rib using same
- Summary
- Abstract
- Description
- Claims
- Application Information
AI Technical Summary
Benefits of technology
Problems solved by technology
Method used
Image
Examples
example 1
Fabrication of a Two-Layered Barrier Rib for an Inkjet Printing Color Filter, which has a Hydrophilic Lower Layer and a Hydrophobic Upper Layer, Through a UV Embossing Process
[0054] A monomer mixture liquid of 70 wt % aliphatic urethane-acrylate telechelic oligomer (Ebecryl 284 manufactured by UCB, Inc.) and 30 wt % hexanediol diacrylate (HDDA manufactured by UCB, Inc.), which had viscosity of 10,000 mPa·sec, as a solvent-free hydrophilic UV-curable material, was mixed with 0.75 wt % bisacylphosphine oxide (BAPO) as a photoinitiator based on the total monomer mixture liquid, and the resulting mixture was applied on a glass substrate having a thickness of 0.7 mm at 500 rpm for 30 sec to form an ink-philic layer (lower layer) having a thickness of 8 μm. 2,2,3,3-tetrafluoropropyl methacrylate monomer (viscosity of 10 mPa·sec) as hydrophobic UV curable material, which contained 0.1 wt % solvent-free fluorine-based surfactant (FC-430 manufactured by 3M Co.) and 1.0 wt % BAPO, was blade ...
example 2
Fabrication of a Barrier Rib for an Inkjet Printing OLED, which has a Hydrophobic Lower Layer and a Hydrophilic Upper Layer, Through a UV / Hot Embossing Process
[0055] A surface of a mold was coated with a fluorine-based surfactant (Zonyl manufactured by DuPont, Inc.) and baked at 200□ so as to have a hydrophobic property. Poly(2,2,3,3-tetrafluoropropyl methacrylate) having a molecular weight of 100,000 (a glass transition temperature of about 66° C.) was dissolved in methylisobutylketone (MIBK) so as to have a concentration of 5 wt %, and applied on a glass substrate using a spin coater at a rotation rate of 2000 rpm to form a lower layer. 2-hydroxyethyl methacrylate oligomer, which was produced by dissolving Irgacure 184 and polymerizing it through UV polymerization until the viscosity was 1,000 mPa·sec, was applied thereon at a rotation rate of 2000 rpm. Subsequently, the mold for fabricating a barrier rib according to the present invention was brought into close contact with the ...
example 3
Fabrication of a Barrier Rib for an Inkjet Printing OLED, which has A Hydrophobic Lower Layer and a Hydrophilic Upper Layer, Through a UV Embossing Process
[0056] The surface of a mold was coated with a fluorine-based surfactant (Zonyl manufactured by DuPont, Inc.) and baked at 200° C. so as to have a hydrophobic property. ORMOCER B59 manufactured by Microresist Co., that is, hydrophobic organic / inorganic hybrid UV curable resin, was applied on a glass substrate using a spin coater at a rotation rate of 3000 rpm. 2-hydroxyethyl methacrylate (HEMA) monomer containing Irgacure 184 was applied thereon in drops of 1 ml using a pipette. Subsequently, the mold for fabricating a barrier rib according to the present invention was brought into close contact with the entire surface of an upper layer, embossing was conducted at room temperature and pressure of 5 kgf / cm2, the backside of the glass substrate was exposed to UV of 1 kW for 3 min using a UV exposing machine, and the mold was remove...
PUM
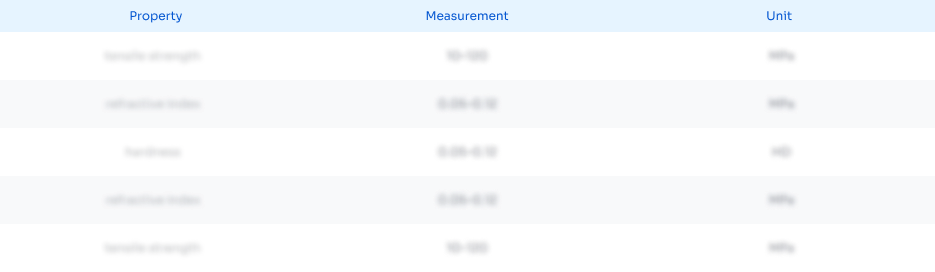
Abstract
Description
Claims
Application Information

- R&D
- Intellectual Property
- Life Sciences
- Materials
- Tech Scout
- Unparalleled Data Quality
- Higher Quality Content
- 60% Fewer Hallucinations
Browse by: Latest US Patents, China's latest patents, Technical Efficacy Thesaurus, Application Domain, Technology Topic, Popular Technical Reports.
© 2025 PatSnap. All rights reserved.Legal|Privacy policy|Modern Slavery Act Transparency Statement|Sitemap|About US| Contact US: help@patsnap.com