Method and device for vibration control
- Summary
- Abstract
- Description
- Claims
- Application Information
AI Technical Summary
Benefits of technology
Problems solved by technology
Method used
Image
Examples
example 1
[0085] In this example, a vibration control system was designed to determine certain parameters of functional requirements of a gantry active control system. The funtional requirements defined included (but were not limited to) the following: [0086] Accuracy [0087] Settling time [0088] Mass, size and location of the actuators and sensors [0089] Power [0090] Peak strains [0091] Lifetime [0092] Temperature range [0093] Exposure to humidity and solvents [0094] Cost [0095] Interfaces with existing gantry control system
[0096] In order to gather data on the structural response of a gantry during operation, the gantry was equipped with an array of piezoelectric strain sensors and accelerometers. Placement and sizing of the piezoelectric actuators required accurate strain mode shape information, which were obtained from this data, and were compared to the Finite Element Model (“FEM”). One important piece of information obtained in this phase of the project involved the effect of different ...
example 2
[0111] A vibration control system in accordance with the invention was used in a lithography machine. As shown in FIG. 16, which shows the power spectral density of error signals recorded by a laser metrology system, use of the vibration control system resulted in a three-fold reduction in system response in the band from 75 to 125 Hz. The reduction in the peak using the vibration control system would be expected to reduce the system image blur by a factor of two-three after conventional methods are used to reduce peaks at 50 Hz and 225 Hz. Alternatively, in some cases, the vibration control system might be used to reduce the peaks at 50 Hz or 225 Hz or at other levels. Reducing the image blur allows the fabrication system to produce finer trace dimensions and feature sizes and improves the accuracy of the feature placement.
PUM
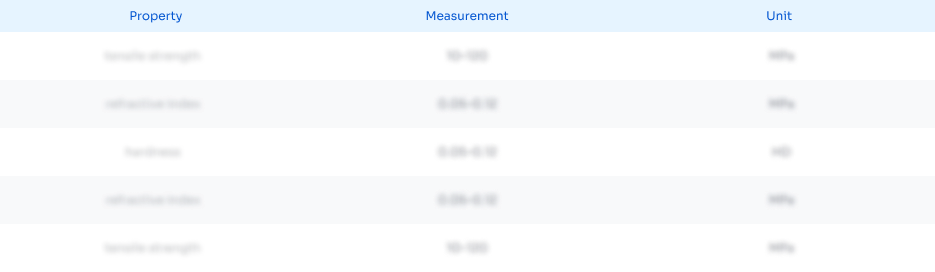
Abstract
Description
Claims
Application Information

- R&D
- Intellectual Property
- Life Sciences
- Materials
- Tech Scout
- Unparalleled Data Quality
- Higher Quality Content
- 60% Fewer Hallucinations
Browse by: Latest US Patents, China's latest patents, Technical Efficacy Thesaurus, Application Domain, Technology Topic, Popular Technical Reports.
© 2025 PatSnap. All rights reserved.Legal|Privacy policy|Modern Slavery Act Transparency Statement|Sitemap|About US| Contact US: help@patsnap.com