Telescopic support tower
a technology of support towers and telescopic beams, which is applied in the direction of girders, machines/engines, mechanical equipment, etc., can solve the problems of high rental costs for heavy lifting cranes, increased material installation costs, and increased labor costs, so as to prevent sway and reduce the cost of erection. , the effect of preventing sway
- Summary
- Abstract
- Description
- Claims
- Application Information
AI Technical Summary
Benefits of technology
Problems solved by technology
Method used
Image
Examples
Embodiment Construction
[0035] Although a preferred embodiment and alternative lift mechanisms for vertically extending the tower are disclosed and explained in detail, it is to be understood that the embodiment and alternatives are given by way of illustration only. It is not intended that the invention be limited in its scope to the details or sequence of construction and arrangement of components set forth in the following description or illustrated in the drawings. Also, in describing the preferred embodiment specific terminology will be utilized for the sake of clarity. It is to be understood that each specific term includes all technical equivalents that operate in a similar manner to accomplish a similar purpose.
[0036] Referring to FIGS. 1A-1F of the drawings, an extended sectional telescopic tower and turbine generator assembly is illustrated in FIG. 1F and generally designated by reference numeral 10. FIGS. 1A-1F illustrate schematically the steps in assembling three tower sections 12, 14, and 16...
PUM
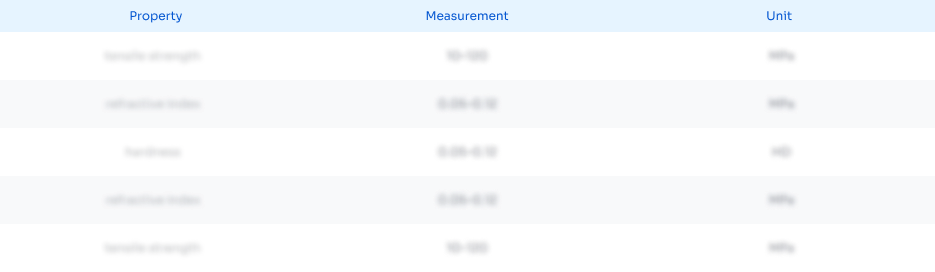
Abstract
Description
Claims
Application Information

- R&D
- Intellectual Property
- Life Sciences
- Materials
- Tech Scout
- Unparalleled Data Quality
- Higher Quality Content
- 60% Fewer Hallucinations
Browse by: Latest US Patents, China's latest patents, Technical Efficacy Thesaurus, Application Domain, Technology Topic, Popular Technical Reports.
© 2025 PatSnap. All rights reserved.Legal|Privacy policy|Modern Slavery Act Transparency Statement|Sitemap|About US| Contact US: help@patsnap.com