Conductive adhesive interconnection with insulating polymer carrier
a technology of conductive adhesive and polymer carrier, which is applied in the direction of printed circuit aspects, sustainable manufacturing/processing, final product manufacturing, etc., can solve the problems of reducing the ability of strain absorption, not alleviating the strain of cte mismatch, and not being compatible with electronic assemblies requiring or desiring the ability of component reworkability, etc., to achieve greater strain absorption, reduce silver migration, and improve the effect of reliability
- Summary
- Abstract
- Description
- Claims
- Application Information
AI Technical Summary
Benefits of technology
Problems solved by technology
Method used
Image
Examples
Embodiment Construction
)
[0039] In describing the preferred embodiment of the present invention, reference will be made herein to FIGS. 1-6 of the drawings in which like numerals refer to like features of the invention. Features of the invention are not necessarily shown to scale in the drawings.
[0040] Manufacturers of printed circuit boards typically have to work with a selection of chip modules having different configurations of electrical connectors as well as different arrangements of the electrical connector footprints for connection to the corresponding contacts on the printed circuit boards. As used herein, the terms "contact arrangement" or "connector arrangement" refers to the pattern of the individual connectors or contacts, including the number and location of such contacts or connectors. As used herein, the term "contact configuration" or "connector configuration" refers to the type of physical and electrical connector utilized between the chip module and the printed circuit board, for example,...
PUM
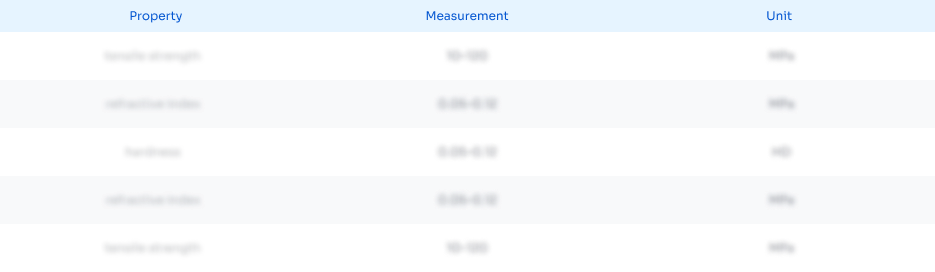
Abstract
Description
Claims
Application Information

- R&D
- Intellectual Property
- Life Sciences
- Materials
- Tech Scout
- Unparalleled Data Quality
- Higher Quality Content
- 60% Fewer Hallucinations
Browse by: Latest US Patents, China's latest patents, Technical Efficacy Thesaurus, Application Domain, Technology Topic, Popular Technical Reports.
© 2025 PatSnap. All rights reserved.Legal|Privacy policy|Modern Slavery Act Transparency Statement|Sitemap|About US| Contact US: help@patsnap.com