Prepn process of 2,5-dichloro-p-phenylenediamine
A technology of dichloro-p-phenylenediamine and dichloroaniline, which is applied in two fields, can solve the problems of unfavorable environmental protection and low total yield of four-step reaction, and achieve the effects of low cost, low production cost, and reduced production cost
- Summary
- Abstract
- Description
- Claims
- Application Information
AI Technical Summary
Problems solved by technology
Method used
Image
Examples
Embodiment 1
[0031] Embodiment 1 2, the preparation of 5-dichloro-p-phenylenediamine
[0032] (a) Acylation of 2,5-dichloroaniline
[0033] Add 30 grams (0.3 mol) of 99% 1,2-dichloroethane into a 250ml four-neck flask equipped with stirring, reflux condenser, and thermometer, and add 10.3 grams (0.062 mol) of 98% 2,5-dichloroaniline under stirring. mol), after 2,5-dichloroaniline is dissolved, add 7.2 grams (0.069mol) of acetic anhydride dropwise at room temperature, raise the temperature to 70-80°C and react for one hour, then add 50ml of water, and distill 1,2-dichloroaniline The azeotrope of ethane and water, the recovered 1,2-dichloroethane 27.4 grams (91.3% recovery rate) can be used mechanically in the next reaction. When the temperature rose to 95°C, the heating was stopped, and the reactant was cooled to room temperature. Filter, wash the filter cake, drain and dry at 75-80°C to obtain 12.6 g of 2,5-dichloroacetanilide with a yield of 98%, a purity of 99.3% as determined by HPLC,...
Embodiment 2
[0041] Embodiment 2 2, the acylation test of 5-dichloroaniline
[0042] Add 42 grams (0.32mol) of 95% 1,1,1-trichloroethane into a 250ml four-neck flask equipped with stirring, reflux condenser, and thermometer, and add 10.3 grams of 98% 2,5-dichloroaniline under stirring (0.062mol), after 2,5-dichloroaniline was dissolved, 7.2 grams (0.069mol) of acetic anhydride was added dropwise at room temperature, and the temperature was raised to 70-80°C to react for one hour, then 80ml of water was added, and 1,1 was evaporated. The azeotrope of 1-trichloroethane and water, the recovered 1,1,1-trichloroethane can be recycled and used mechanically. When the temperature rose to 90°C, the heating was stopped, and the reactant was cooled to room temperature. Filter, wash the filter cake, drain and dry at 75-80°C to obtain 12.4 g of 2,5-dichloroacetanilide with a yield of 97%, a purity of 99.2% by HPLC, and a M.P. of 134-135°C.
Embodiment 3
[0043] The reduction test of embodiment 3 4-nitro-dichloroaniline
[0044] Weigh respectively 6.4 grams (0.03mol) of 4-nitro-2,5-dichloroaniline, 128 grams (2.64mol) of 95% ethanol, 1.2 grams of ferric chloride and activated carbon (mass ratio 1: 5), and put into In a 250ml four-neck flask equipped with a stirring, reflux condenser, and a thermometer, stir and heat up to reflux, add 3.6 grams (0.061mol) of 85% hydrazine hydrate, and keep refluxing for two hours. Cool to 60°C and filter, collect the filtrate and distill ethanol out (ethanol recovery is applied mechanically, the recovery rate is 80%), add an appropriate amount of water to the material, cool and crystallize, filter, wash and drain, and dry at 78-80°C to obtain 2. 3.0 g of 5-dichloro-p-phenylenediamine, 93% yield, 99.6% measured by HPLC, M.P.164-165°C.
PUM
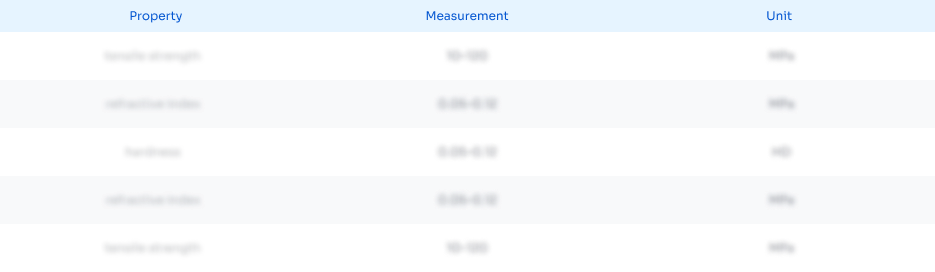
Abstract
Description
Claims
Application Information

- R&D
- Intellectual Property
- Life Sciences
- Materials
- Tech Scout
- Unparalleled Data Quality
- Higher Quality Content
- 60% Fewer Hallucinations
Browse by: Latest US Patents, China's latest patents, Technical Efficacy Thesaurus, Application Domain, Technology Topic, Popular Technical Reports.
© 2025 PatSnap. All rights reserved.Legal|Privacy policy|Modern Slavery Act Transparency Statement|Sitemap|About US| Contact US: help@patsnap.com