Agent for reducing coating film overall friction coefficient for trivalent chromate treating solution, trivalent chromate treating solution and method for production thereof, and trivalent chromate co
A technology of trivalent chromate and treatment solution, applied in the direction of metal material coating process, etc., to achieve the effect of safe fastening strength, excellent corrosion resistance, and maintaining productivity
- Summary
- Abstract
- Description
- Claims
- Application Information
AI Technical Summary
Problems solved by technology
Method used
Examples
Embodiment 1 to 18
[0067] Zinc (zincate bath (NZ-87, available from Dipsol Chemicals Co., Ltd.), cyanide bath (L-800, available from Dipsol Chemicals Co., Ltd.), chloride M6 bolts (S45C material, strength division 8.8) in a bath (EZ-988, available from Dipsol Chemicals Co., Ltd.) were immersed in trivalent chromic acid having the compositions shown in Tables 1 and 2 below Salt treatment solution, then rinse with water.
[0068] Example number
[0069] Example number
[0070] In Tables 1 and 2, the Cr 3+ Source is CrCl 3 (in Examples 1, 3, 5, 8, 10, 15 and 18) and Cr(NO 3 ) 3 (in Examples 2, 4, 6, 7, 9, 11 to 14, 16 and 17); the oxalic acid used was dihydrate; the Co source used was Co(NO 3 ) 2 . In addition, the Si source used is silica gel; the V source used is VOSO 4 ; The Ni source used was NiSO 4 . Further, the NO used 3 - Source is HNO 3 (in Examples 2, 3, 4, 9 to 11, 14, 15 and 18) and NaNO 3 (in Examples 1, 5 to 7, 12, 13, 16 and 17). Further, the Cl used...
Embodiment 19 to 22
[0072] Alkaline Zn-Ni alloys ((IZ-262 (Ni: 7%), available from Dipsol Chemicals Co., Ltd., IZ-252 (Ni: 14%), available from Dipsol Chemicals Co., Ltd., each plated with a thickness of 8 μm, were M6 bolts (S45C material, strength scale 8.8) obtained from Chemicals Co., Ltd.)) were dipped in a trivalent chromate treatment solution having the composition shown in Table 3 below, and then washed with water.
[0073] Example number
[0074] In Table 3, the Cr 3+ The source is Cr(NO 3 ) 3 (in Examples 15 and 17) and CrCl 3 (in Examples 16 and 18); the oxalic acid used was dihydrate; the Co source used was Co(NO 3 ) 2 . Furthermore, the Si source used was silica gel; the Ni source used was NiSO 4 . Further, NO 3 - Source is NaNO 3 ;Cl used - The source is NaCl; the PO used 4 - Source is NaH 2 PO 4 . The balance of each treatment solution was water. In addition, the pH of each solution was adjusted using NaOH.
Embodiment 23
[0100] When the conversion coating was formed on the bolts using the trivalent chromate treatment solution of Example 1, the resulting overflow was transferred to a backup tank. The pumping speed is 800L / hour. Next, quinallidinic acid was added to the treatment solution in the spare tank so that its concentration in the treatment solution was 8 g / L, and then the resulting treatment solution was returned through a filter (K-05, available from Kizai Company) into the treatment tank. Therefore, the concentration of quinaldicic acid in the treatment solution present in the treatment tank can be kept constant.
PUM
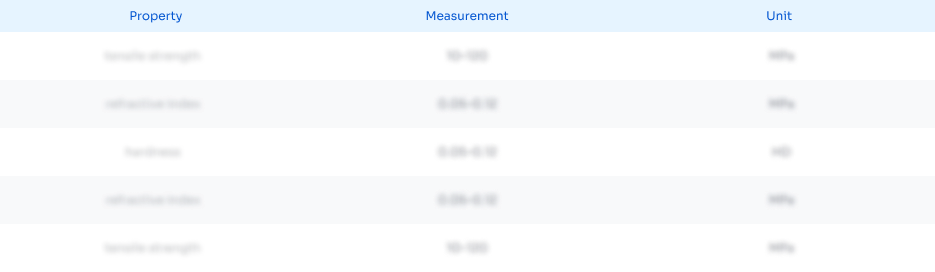
Abstract
Description
Claims
Application Information

- Generate Ideas
- Intellectual Property
- Life Sciences
- Materials
- Tech Scout
- Unparalleled Data Quality
- Higher Quality Content
- 60% Fewer Hallucinations
Browse by: Latest US Patents, China's latest patents, Technical Efficacy Thesaurus, Application Domain, Technology Topic, Popular Technical Reports.
© 2025 PatSnap. All rights reserved.Legal|Privacy policy|Modern Slavery Act Transparency Statement|Sitemap|About US| Contact US: help@patsnap.com