Heat exchanger for fuel oil heater with heat exchange pipe
A fuel-fired heater and heat exchanger technology, applied in fluid heaters, lighting and heating equipment, etc., can solve the problems of limited heat exchange area, excessive heat loss, and inability to obtain high enough thermal efficiency, and reduce production and technology. Retrofit cost, improved thermal efficiency, and effect of shortened warm-up time
- Summary
- Abstract
- Description
- Claims
- Application Information
AI Technical Summary
Problems solved by technology
Method used
Image
Examples
Embodiment 1
[0021] Figure 1 shows the structure of this embodiment, including heat exchange body 4, heat transfer fin 5, spiral guide fin 3, bottom plate 8, heat exchange body shell 1, water inlet pipe 13, water outlet pipe 6, plug 7, spacer Plate 10 and heat exchange tube 9. The inner wall of the heat exchange body 4 is welded with heat transfer fins 5 distributed along the circumferential direction, and each heat transfer fin is welded along the axial direction. The outer wall of the heat exchanging body 4 is welded with a spiral guide fin 3 , and the cross section of the spiral guide fin 3 can be rectangular, triangular, trapezoidal or circular. The bottom of the heat exchange body 4 is welded with a bottom plate 8 to seal the heat exchange body 4 and isolate the high-temperature gas in the combustion chamber from the circulating water. The heat exchange tube 9 is installed on the bottom plate 8 and is on the high temperature gas side. The shell 1 is set on the outside of the heat ex...
Embodiment 2
[0024] Figure 3 shows the structure of this embodiment. The difference between this embodiment and Embodiment 1 is that the heat exchange tubes 9 in this embodiment are connected in series at the end of the spiral water chamber in parallel at a certain interval in the flame cylinder. , each heat exchange tube is perpendicular to the bottom plate 8, as shown in FIG. 4 . The partition 10 is close to the upper edge of the water inlet of the heat exchange tube, and is connected with the bottom plate 8 and the plug 7. A water outlet chamber is formed above the partition, and a water inlet chamber is formed below. The partition plate 10 can be arranged horizontally as a straight plate, or can be arranged with a slightly higher slope at the end of the bypass hole 14, so as to facilitate exhaust.
Embodiment 3
[0026] FIG. 5 shows the structure of this embodiment. The difference between this embodiment and Embodiment 1 and Embodiment 2 is that this embodiment uses a spiral heat exchange tube 9 , as shown in FIGS. 5 and 6 . The center of the spiral tube coincides with the axis of the burner flame tube 11, the water inlet end is located at the center of the bottom plate 8, and the partition plate 10 is close to the upper edge of the water inlet of the heat exchange tube and connected with the bottom plate 8 and the plug 7 to form the water inlet and outlet. cavity.
[0027] In a specific application, if the flame flow section of the burner flame tube is constant, when there are too many heat exchange tubes or the tube diameter is too thick, the high-temperature gas flow resistance will increase and the back pressure will increase, thus affecting the normal combustion of the burner . At this time, the number of heat exchange tubes can be appropriately reduced or the diameter of the hea...
PUM
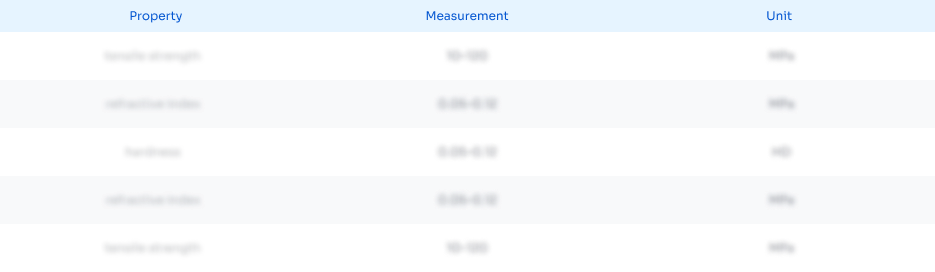
Abstract
Description
Claims
Application Information

- R&D
- Intellectual Property
- Life Sciences
- Materials
- Tech Scout
- Unparalleled Data Quality
- Higher Quality Content
- 60% Fewer Hallucinations
Browse by: Latest US Patents, China's latest patents, Technical Efficacy Thesaurus, Application Domain, Technology Topic, Popular Technical Reports.
© 2025 PatSnap. All rights reserved.Legal|Privacy policy|Modern Slavery Act Transparency Statement|Sitemap|About US| Contact US: help@patsnap.com