Ultrathin soaking plate and manufacturing method thereof
A manufacturing method and vapor chamber technology, applied in the direction of indirect heat exchangers, lighting and heating equipment, etc., can solve the problems of difficulty in further reducing the thickness of vapor chamber, complicated manufacturing process, and complicated manufacturing process, and achieve low cost and increased Effect of increased surface area and heat transfer area
- Summary
- Abstract
- Description
- Claims
- Application Information
AI Technical Summary
Problems solved by technology
Method used
Image
Examples
Embodiment 1
[0042] like Figure 1~5 As shown, it is an ultra-thin vapor chamber of the present invention, which includes a cover plate 1 and a bottom plate 2 that are sealed and connected at the periphery. A groove 12 is provided on the inner surface of the cover plate 1 to make the gap between the cover plate 1 and the bottom plate 2 A cavity 8 in a vacuum state is formed. In this embodiment, the bottom plate 2 is a flat plate, and the edge of the cover plate 1 is turned outward into a hem 11. In the cavity 8 and on the bottom surface of the groove 12, there are several Protrusions 3 arranged in an array, the protrusions 3 are hollow columns formed by pressing, the bottom surface of the protrusions 3 is flush with the lower surface of the flange 11, and the periphery of the bottom plate 1 is welded on the flange of the cover plate 2 to connect the cover plate 1 And the bottom plate 2, the protrusion 3 connects the cover plate 1 and the bottom plate 2 to support between the cover plate 1 ...
Embodiment 2
[0055] Such as Image 6 As shown, the difference between the ultra-thin vapor chamber of this embodiment and the ultra-thin vapor chamber of Embodiment 1 is that three or four protrusions 3 are close to each other to form a local void unit 6 with a hole 7 in the middle, which is relatively There are gaps between adjacent protrusions 3 , and each local gap unit 6 is distributed in an array. The diameter of the local void unit is 0.1-1mm.
[0056] The manufacturing process of this embodiment differs from the manufacturing process of Embodiment 1 in that: the specific position of the protrusions 3 on the metal sheet is different, so as to form three or four protrusions 3 close to each other to form a local void with a channel 7 in the middle unit 6, and each local void unit 6 is in the form of an array distribution.
Embodiment 3
[0058] Such as Figure 7 As shown, the difference between the ultra-thin vapor chamber of this embodiment and the ultra-thin vapor chamber of embodiment 2 is that a capillary structure is laid on the inner surface of the bottom plate 2, and the capillary structure can be copper powder or copper mesh 5, In other embodiments, other capillary structures can also be used, and the protrusion 3 presses down on the capillary structure and is welded together with the capillary structure and the bottom plate 2 . The inner surface of the cavity is coated with a hydrophilic coating, that is, the outer wall of the protrusion, the top surface of the cavity and the copper mesh 5 are coated with a hydrophilic coating. The copper mesh absorbs the working fluid and has a siphon phenomenon. It can increase the heating and heat exchange area and increase the heat dissipation efficiency.
[0059] The manufacturing process of this embodiment is different from the manufacturing process of Example ...
PUM
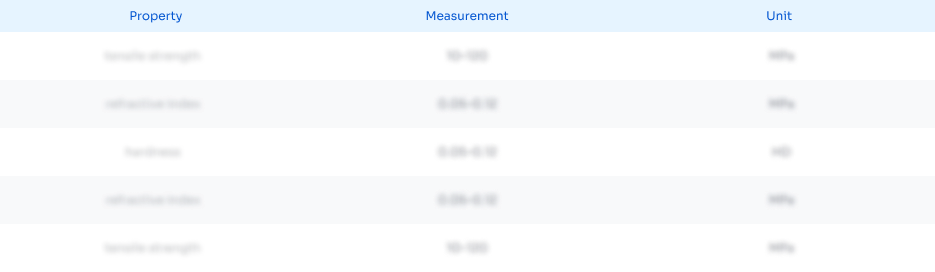
Abstract
Description
Claims
Application Information

- R&D
- Intellectual Property
- Life Sciences
- Materials
- Tech Scout
- Unparalleled Data Quality
- Higher Quality Content
- 60% Fewer Hallucinations
Browse by: Latest US Patents, China's latest patents, Technical Efficacy Thesaurus, Application Domain, Technology Topic, Popular Technical Reports.
© 2025 PatSnap. All rights reserved.Legal|Privacy policy|Modern Slavery Act Transparency Statement|Sitemap|About US| Contact US: help@patsnap.com