Method for preparing high coercive force sintering rare-earth-iron-p permanent magnetic material
A high-coercivity, permanent-magnet material technology, applied in the field of magnetic materials, can solve the problems of high-coercivity magnet's shape and size limitation, and the technology has not been reported. Effect
- Summary
- Abstract
- Description
- Claims
- Application Information
AI Technical Summary
Problems solved by technology
Method used
Examples
Embodiment 1
[0017] Use quick-setting technology to change the composition to Nd 30.0 Fe 67.5 co 1.4 B 1.1 (mass percentage content) of the alloy is prepared as flakes, and then the powder is made into a powder with an average particle size of 3 microns by using a hydrogen crushing-jet milling process. (referring to Chinese patent in detail: 93115008.6, patent name: rare earth-iron-boron permanent magnet material and the preparation method of this material, announcement date: on January 10th, 1996, publication number: CN 1114779A, following embodiment is the same, just existing The one common to the technology is not limited to that technology).
[0018] Afterwards, 1% by weight of terbium nano-powder with an average particle size of 10 nanometers (the detailed process of nano-powder preparation can refer to the patent applied by this research group in the early stage: 200510089080.3 Authorized announcement date: 2006.3.8, publication number: CN 1743103 Patent name: Rare earth nanopart...
Embodiment 2
[0026] Use quick-setting technology to change the composition to Nd 30.0 Fe 67.5 co 1.4 B 1.1 (mass percentage content) of the alloy is prepared as flakes, and then the powder is made into a powder with an average particle size of 4 microns by using a hydrogen crushing-jet milling process. Then, 3% by weight of dysprosium nanopowder with an average particle size of 30 nanometers was added to the above-mentioned initial powder, and the two powders were uniformly mixed by a mixer. The uniformly mixed powder was oriented in a magnetic field of 2.5T and pressed into shape. Then put the compact into a high vacuum sintering furnace, sinter at 1080°C for 3 hours, and then perform secondary heat treatment, wherein the primary heat treatment temperature is 900°C for 3 hours; the secondary heat treatment temperature is 700°C for 1 hr. That is, a sintered magnet was obtained. The magnetic properties and densities of the prepared magnets are listed in Table 2.
Embodiment 3
[0032] Use quick-setting technology to change the composition to Nd 30.0 Fe 67.5 co 1.4 B 1.1 (mass percentage content) of the alloy is prepared as flakes, and then the powder is made into a powder with an average particle size of 3 microns by using a hydrogen crushing-jet milling process. Then, 1% by weight of dysprosium nanopowder with an average particle size of 20 nanometers was added to the above-mentioned initial powder, and the two powders were uniformly mixed by a mixer. The uniformly mixed powder was oriented in a magnetic field of 2.5T and pressed into shape. Then put the compact into a high vacuum sintering furnace, sinter at 1100°C for 2 hours, and then perform secondary heat treatment, wherein the primary heat treatment temperature is 1000°C for 1 hr; the secondary heat treatment temperature is 550°C for 3 hr. That is, a sintered magnet was obtained. The magnetic properties and densities of the prepared magnets are listed in Table 3.
[0033] Terbiu...
PUM
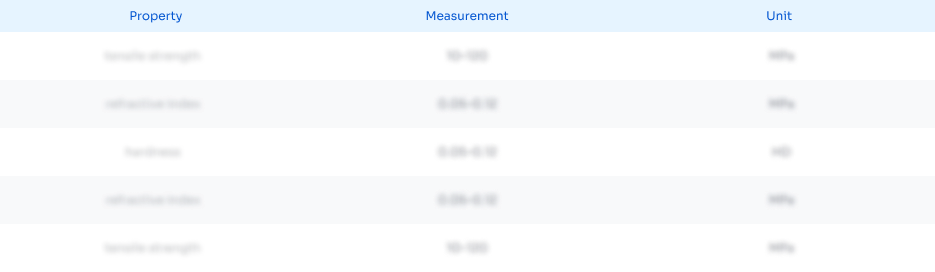
Abstract
Description
Claims
Application Information

- R&D
- Intellectual Property
- Life Sciences
- Materials
- Tech Scout
- Unparalleled Data Quality
- Higher Quality Content
- 60% Fewer Hallucinations
Browse by: Latest US Patents, China's latest patents, Technical Efficacy Thesaurus, Application Domain, Technology Topic, Popular Technical Reports.
© 2025 PatSnap. All rights reserved.Legal|Privacy policy|Modern Slavery Act Transparency Statement|Sitemap|About US| Contact US: help@patsnap.com