High-temperature reparation glaze composition and process for preparing same and application thereof
A technology for repairing glaze and composition, applied in the material field of the ceramic field, can solve the problems of no silky luster, rough surface, peeling, etc., achieve smooth glaze without cracks and peeling, and prevent the secondary firing temperature from being too high. The effect of high and low firing temperature
- Summary
- Abstract
- Description
- Claims
- Application Information
AI Technical Summary
Problems solved by technology
Method used
Image
Examples
Embodiment 1
[0064] Preparation of the repair glaze composition: the repair glaze composition was prepared by wet ball milling.
[0065] The repair glaze is composed of the base glaze of the original ceramic and the transparent frit. According to the components and contents shown in Table 1 and Table 2, the raw material mixtures A1-A5 of the basic glaze and transparent frit were prepared respectively, and water and electrolyte were added: sodium silicate water glass 0.03-0.05% and organic polymer diluent P132 0.35- 0.5%, into a ball mill for ball milling until the specific gravity is 1800-1850, preferably 1830-1840, and the particle weight is less than 1.5% with a fineness of 32 μm or more.
[0066] repair glaze
SiO 2
al 2 o 3
Fe 2 o 3
RO
R 2 o
ZrO 2
BaO
B 2 o 3
total
base glaze
52.8
11.0
0.1
8
4.3
7.6
5.4
10.8...
Embodiment 2
[0073] Glazing process and firing process:
[0074] (3) The repair glaze is sprayed with a spray gun (adjustable pressure of 0-10bar). The performance parameters of the glaze slurry are: Brookfield viscosity CP = 1800-1900, and yield value = 35 ± 3, using organic polymer liquid Quick desiccant ZS adjustment;
[0075] (4) glaze spraying method;
[0076] (5) Firing process: for repaired ceramic products, the maximum firing temperature is 1180-1200°C, and after 10-20 hours of firing, the maximum firing temperature is controlled to be lower than the maximum firing temperature of the base glaze by 30-50°C. That is, if the firing temperature of the base glaze is 1210-1230°C, the maximum firing temperature of the repair glaze is 1160-1200°C. For example: if the firing temperature of the base glaze is 1221°C, the firing temperature for repairing is 1180°C.
[0077] temperature
Fineness (32μm)
Brookfield viscosity CP
Yield value
Glazing...
Embodiment 3
[0081] Using the thermal dilatometer method, measure the expansion curves of the high-temperature repair glaze and the basic glaze on a thermal dilatometer (model Dil804L), the results are as follows figure 1 shown. The data analysis results show that the ratio range of the expansion coefficient of the high-temperature repair glaze composition to the base glaze at a firing temperature of 120-830°C=the expansion coefficient of the repair glaze÷the expansion of the base glaze×100%=100%±13%.
PUM
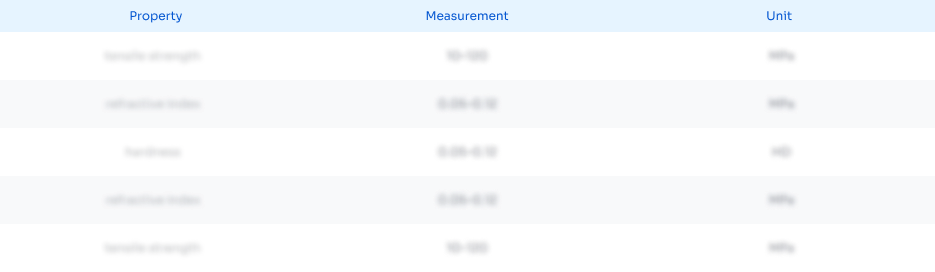
Abstract
Description
Claims
Application Information

- Generate Ideas
- Intellectual Property
- Life Sciences
- Materials
- Tech Scout
- Unparalleled Data Quality
- Higher Quality Content
- 60% Fewer Hallucinations
Browse by: Latest US Patents, China's latest patents, Technical Efficacy Thesaurus, Application Domain, Technology Topic, Popular Technical Reports.
© 2025 PatSnap. All rights reserved.Legal|Privacy policy|Modern Slavery Act Transparency Statement|Sitemap|About US| Contact US: help@patsnap.com