Sintered ferrovanadium alloy and its prepn process
A technology of vanadium-iron alloy and vanadium compound, which is applied in the field of preparing sintered vanadium-iron alloy, can solve the problems of complex process, long preparation process, and low vanadium effective yield, and achieve the goal of simplifying the preparation process, saving aluminum alloy consumption, and improving labor productivity Effect
- Summary
- Abstract
- Description
- Claims
- Application Information
AI Technical Summary
Problems solved by technology
Method used
Examples
Embodiment 1
[0036] Put 1000 grams of vanadium oxide containing 54.1% vanadium, 250 grams of graphite powder, and 142 grams of iron powder into a ball mill to pulverize and mix them, pass through a 80-mesh screen, add 105 ml of 1.5% cellulose aqueous solution, mix evenly and briquette, and press into The briquette of Φ20*20 is dried at 120°C for 3 hours, and then put into a carbon tube furnace protected by ammonia gas for carbothermal reduction and sintering reaction. The temperature in the first section is 1100 degrees, and the temperature in the second section is 1430 degrees. The mixture briquette stays in the second stage for 3 hours, the ammonia gas flow rate in the furnace is controlled to be 30-60 Pa higher than the pressure outside the furnace, and the ammonia dew point is -40 degrees. After the reaction, it was cooled to 150°C under the protection of ammonia gas and released from the furnace.
[0037] The obtained sintered vanadium ferroalloy product composition:
[0038] V: 78....
Embodiment 2
[0042] Put 1,000 grams of vanadium oxide powder containing 54.1% vanadium, 205 grams of graphite powder, and 563 grams of iron powder, mix and ball mill, pass through an 80-mesh sieve, add 120ml of cellulose aqueous solution containing 1.5%, mix and briquetting, and press into φ20 *20 material blocks, after drying at 110°C for 2.5 hours, put them into a muffle sintering furnace with nitrogen gas at a temperature of 800°C to 1380°C for carbothermal reduction and sintering reaction, and hold at 1380°C for 2 hours Hour. Cool down with furnace protection to below 250°C and release from the furnace. The flow rate of nitrogen gas is to protect the pressure inside the furnace to be 30-70 Pa higher than the pressure outside the furnace, and the nitrogen dew point is -40 degrees.
[0043] The composition of the obtained sintered vanadium ferroalloy:
[0044] V: 48.1%, Fe: 50.96%, C: 0.19%, P: 0.0596, S<0.01%. Si: 0.84%, Mn: 0.32%, Al: 0.05%,
[0045] Its product density: 6.74 g / cm ...
Embodiment 3
[0047]Mix and grind 1,000 grams of oxide powder containing 64.1% vanadium, 167 grams of graphite powder, and 618 grams of iron powder, pass through an 80-mesh sieve, add 150 ml of cellulose solution containing 1.5%, mix well, and press into a φ20 *20 blocks are dried at 110°C for 3 hours and then placed in a sintering furnace protected by decomposing ammonia gas. The dew point of ammonia gas is -40°C, the temperature of the first stage is 1050-1200°C, and the temperature of the second stage is 1300-1410°C. The second holding time is 4 hours. Cool down to 200°C under the protection of reducing gas to release from the furnace.
[0048] The composition of the obtained sintered ferrovanadium product is:
[0049] V: 50.13%, C: 0.81%, Fe: 48.09%, P: 0.01%, S: 0.02%. Si: 0.71%, Mn: 0.31%, Al: 0.03%,
[0050] Its product density: 6.81 g / cm 3 .
PUM
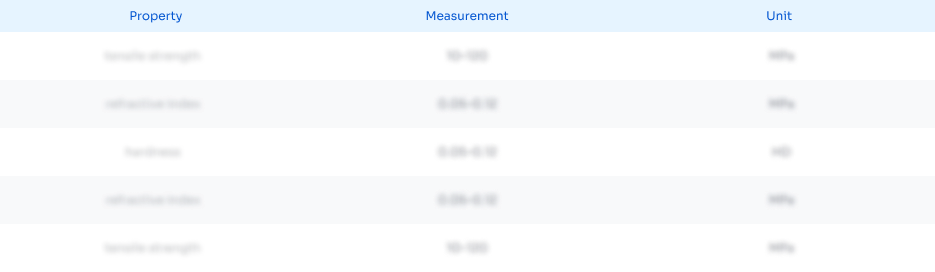
Abstract
Description
Claims
Application Information

- R&D
- Intellectual Property
- Life Sciences
- Materials
- Tech Scout
- Unparalleled Data Quality
- Higher Quality Content
- 60% Fewer Hallucinations
Browse by: Latest US Patents, China's latest patents, Technical Efficacy Thesaurus, Application Domain, Technology Topic, Popular Technical Reports.
© 2025 PatSnap. All rights reserved.Legal|Privacy policy|Modern Slavery Act Transparency Statement|Sitemap|About US| Contact US: help@patsnap.com