Manufacturing method of color filter
The technology of a color filter and manufacturing method, which is applied in the field of color filters, can solve problems such as complicated procedures, low material use efficiency, and high cost of liquid crystal displays, and achieve the effects of preventing color mixing and suppressing loss
- Summary
- Abstract
- Description
- Claims
- Application Information
AI Technical Summary
Problems solved by technology
Method used
Image
Examples
Embodiment Construction
[0023] Hereinafter, preferred embodiments of the present invention will be described with reference to the drawings.
[0024] Figure 1 to Figure 10 It shows an example of embodiment of this invention, and is a figure for demonstrating each process in the manufacturing method of a color filter.
[0025] Before manufacturing a color filter, first, light-shielding banks (banks) of a predetermined pattern are formed on a transparent substrate, for example, a transparent glass substrate. figure 1 It is a schematic perspective view showing the state in which a boss is formed on a glass substrate. figure 2 It is a partial perspective view in which a part is enlarged. figure 1 An example in which six parts are taken is shown, and six effective regions A corresponding to the effective parts of the color filter are provided on one glass substrate 10 .
[0026] The boss 12 is a member that functions as a super black matrix in a color filter, and is made of a light-shielding material...
PUM
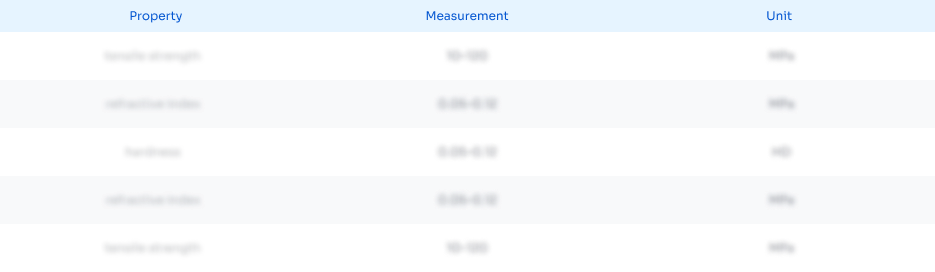
Abstract
Description
Claims
Application Information

- R&D Engineer
- R&D Manager
- IP Professional
- Industry Leading Data Capabilities
- Powerful AI technology
- Patent DNA Extraction
Browse by: Latest US Patents, China's latest patents, Technical Efficacy Thesaurus, Application Domain, Technology Topic, Popular Technical Reports.
© 2024 PatSnap. All rights reserved.Legal|Privacy policy|Modern Slavery Act Transparency Statement|Sitemap|About US| Contact US: help@patsnap.com