Method for improving heavy-current discharge performance of iron phosphate lithium
A high-current discharge, lithium iron phosphate technology, applied in battery electrodes, chemical instruments and methods, circuits, etc., can solve the problems of poor high-current discharge performance, complicated preparation process, and difficulty in industrialization, so as to improve ionic conductivity, The effect of low calcination temperature and low production cost
- Summary
- Abstract
- Description
- Claims
- Application Information
AI Technical Summary
Problems solved by technology
Method used
Image
Examples
Embodiment 1
[0021] Example 1 After fully stirring and mixing an equal volume of 0.1 mol / L ferrous chloride, chromium sulfate mixed solution (the molar ratio of iron and chromium elements is 95:5) and 0.1 mol / L phosphoric acid, add lithium hydroxide to control the pH value is 3.5, then add sodium peroxide to obtain a suspension, the suspension stays in a strongly stirred reactor for 6 hours, then filters and washes, and the obtained filter cake (precursor) is baked at 120° C. for 12 hours. Mix the dried precursor, carbon gel and lithium acetate according to the stoichiometric ratio (the carbon gel is calculated according to the carbon content), and at the same time ensure that the excess carbon gel is 1%, after ball milling for 30 minutes, then put the mixture into the reduction furnace , heated to 500°C, 600°C, 700°C, and 800°C at a heating rate of 2°C / min and held for 20 hours. The obtained material is analyzed by X-ray diffraction as an olivine structure, and the space group is Pnma, wh...
Embodiment 2
[0023] Example 2 After fully stirring and mixing equal volumes of 0.1 mol / L ferrous sulfate and nickel sulfate mixed solution (the molar ratio of iron and nickel elements is 95:5) and 0.1 mol / L sodium dihydrogen phosphate, add ammonia water to control the pH The value is 3.5, then add hydrogen peroxide to obtain a suspension, the suspension stays in a strongly stirred reactor for 6 hours, then filters and washes, and the obtained filter cake (precursor) is baked at 120°C for 12 hours. Mix the dried precursor, carbon black and lithium hydroxide according to the stoichiometric ratio, and at the same time ensure that the excess of carbon black is 1%, after ball milling for 30 minutes, then put the mixture into the reduction furnace, and pass N 2 Gas protection, heating to 600°C at a heating rate of 2°C / min and holding for 10h, 20h and 30h respectively. The obtained material is analyzed by X-ray diffraction as an olivine structure, and the space group is Pnma, which is LiFePO 4 S...
Embodiment 3
[0025]Example 3 Mix equal volumes of 0.1mol / L ferrous acetate and manganese sulfate mixed solution (the molar ratios of iron and manganese elements are respectively 99:1, 97:3, 95:5, 90:10) and 0.1mol / L After ammonium dihydrogen phosphate is fully stirred and mixed, lithium hydroxide is added to control the pH value to 3.5, and then sodium peroxide is added to obtain a suspension, which stays in a strongly stirred reactor for 6 hours, then filtered and washed to obtain The filter cake (precursor) was baked at 120°C for 12 hours. Mix the dried precursor, acetylene black and lithium carbonate according to stoichiometry, and at the same time ensure that the excess of acetylene black is 1%, after ball milling for 30 minutes, then put the mixture into the reduction furnace, and pass through Ar gas protection, at 2°C / min The heating rate is heated to 600 ° C and kept for 20 hours. The obtained material is analyzed by X-ray diffraction as an olivine structure, and the space group is...
PUM
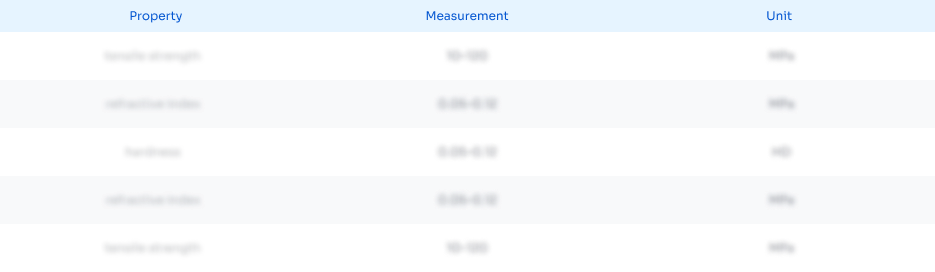
Abstract
Description
Claims
Application Information

- Generate Ideas
- Intellectual Property
- Life Sciences
- Materials
- Tech Scout
- Unparalleled Data Quality
- Higher Quality Content
- 60% Fewer Hallucinations
Browse by: Latest US Patents, China's latest patents, Technical Efficacy Thesaurus, Application Domain, Technology Topic, Popular Technical Reports.
© 2025 PatSnap. All rights reserved.Legal|Privacy policy|Modern Slavery Act Transparency Statement|Sitemap|About US| Contact US: help@patsnap.com