Long nozzle in composite structure free from prewarming
A composite structure, no preheating technology, applied in the direction of casting molten material container, metal processing equipment, casting equipment, etc., can solve the problem that the service life cannot be synchronized, and achieve the effect of good thermal shock resistance and molten steel erosion resistance
- Summary
- Abstract
- Description
- Claims
- Application Information
AI Technical Summary
Problems solved by technology
Method used
Image
Examples
Embodiment 1
[0015] The ingredients of the prepared preheating-free long nozzle outer layer aluminum carbon are 55% of fused white corundum, 14% of sintered alumina powder, 25% of flake graphite, 5% of silicon carbide powder, and 1% of boron carbide. The binder phenolic resin is the total ingredients. 10% by weight; the carbon-free inner layer ingredients are 70% magnesium aluminum spinel, Al 2 o 3 -MgO-TiO 2 Synthetic material 27%, its composition is Al 2 o 3 30%, MgO15%, TiO 2 55%; aluminum-silicon alloy powder 3%, aluminum-silicon sol (Al 2 o 3 Content 20%, SiO 2 Content 5%) is 5% of the total weight of the lining material. Put the above two ingredients in the kneading machine with a binder and knead them evenly. After drying at 70°C, inject them into the rubber sleeve for isostatic pressing. Pressure 140Mpa, keep pressure for 3 minutes. After forming, the green body is heat-treated at 1300°C for 6 hours under a nitrogen atmosphere in a shuttle kiln, and then processed, install...
Embodiment 2
[0017] The aluminum carbon ingredients of the outer layer of the long nozzle are 55% of brown corundum, 14% of sintered alumina powder, 25% of flake graphite, 5% of silicon carbide powder, 1% of boron carbide, and the binder phenolic resin is 10% of the total weight of the ingredients; The carbon-containing inner layer ingredients are 70% fused corundum, Al 2 o 3 -MgO-TiO 2 Synthetic material 25%, its composition is Al 2 o 3 50%, MgO10%, TiO 2 40%; metal aluminum powder 5%, aluminum sol (Al 2 o 3 Content 25%) is 5% of the total weight of the lining material. Add the above two ingredients to the kneading machine and mix them evenly with a binder. After drying at 70°C, inject them into the rubber sleeve for isostatic pressing. 140Mpa, keep the pressure for 3 minutes. After forming, the green body is heat-treated at 1300°C for 3 hours in a nitrogen atmosphere in a shuttle kiln, and then processed, installed with a metal ventilation hood, and painted with anti-oxidation pa...
Embodiment 3
[0019] The outer aluminum carbon ingredients are 55% brown corundum, 14% sintered alumina powder, 25% flake graphite, 5% silicon carbide powder, 1% boron carbide, and 10% of the total weight of the binder phenolic resin; no carbon The inner layer ingredients are magnesium aluminum spinel 25%, Al 2 o 3 -MgO-TiO 2 Synthetic material 70%, its composition is Al 2 o 3 50%, MgO5%, TiO 2 45%; aluminum-magnesium alloy powder 5%, phenolic resin is 8% of the total weight percentage of the lining ingredients. Put the above two ingredients in a kneader with a binder and knead evenly. After drying at 70°C, inject them into the rubber sleeve for isostatic pressing. The main body aluminum carbon material is injected into the outer side, and the inner lining is injected with silicon-free and carbon-free material into the inner side. Pressure 140Mpa, keep pressure for 3 minutes. After forming, the green body is heat-treated at 1200°C for 3 hours under a nitrogen atmosphere in a shuttle k...
PUM
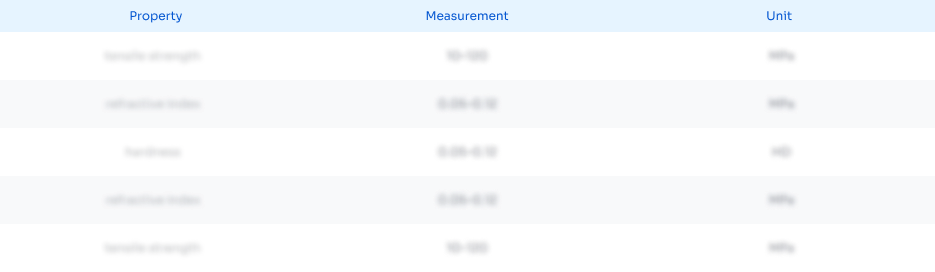
Abstract
Description
Claims
Application Information

- Generate Ideas
- Intellectual Property
- Life Sciences
- Materials
- Tech Scout
- Unparalleled Data Quality
- Higher Quality Content
- 60% Fewer Hallucinations
Browse by: Latest US Patents, China's latest patents, Technical Efficacy Thesaurus, Application Domain, Technology Topic, Popular Technical Reports.
© 2025 PatSnap. All rights reserved.Legal|Privacy policy|Modern Slavery Act Transparency Statement|Sitemap|About US| Contact US: help@patsnap.com