Nickel-saving RE-containing austenitic stainless steel and its prepn
An austenitic and stainless steel technology, applied in the field of austenitic stainless steel and its preparation, can solve the problems of unscientific and reasonable composition design, poor corrosion resistance and high strength, saving precious nickel resources, reducing production costs, comprehensive good performance
- Summary
- Abstract
- Description
- Claims
- Application Information
AI Technical Summary
Problems solved by technology
Method used
Image
Examples
Embodiment Construction
[0049] According to the chemical composition of the nickel-saving austenitic rare earth-containing stainless steel of the present invention, 3 heats of the steel of the present invention were smelted on a non-vacuum induction furnace, and the chemical composition (wt%) of the 3 heats of steel is shown in Table 1. After smelting, it is cast into an ingot, and then the ingot billeting, steel rolling and solution treatment are carried out according to the process steps of its preparation method. The parameters related to smelting, casting, ingot opening, steel rolling and solution treatment are shown in Table 2. Subsequently, the product steel was sampled, and the mechanical performance test and corrosion performance test were carried out respectively, and the obtained results were listed in Table 3 and Table 4 and 5 respectively.
[0050] For comparison, under the same equipment conditions, a furnace of austenitic stainless steel with the same or similar composition as that of t...
PUM
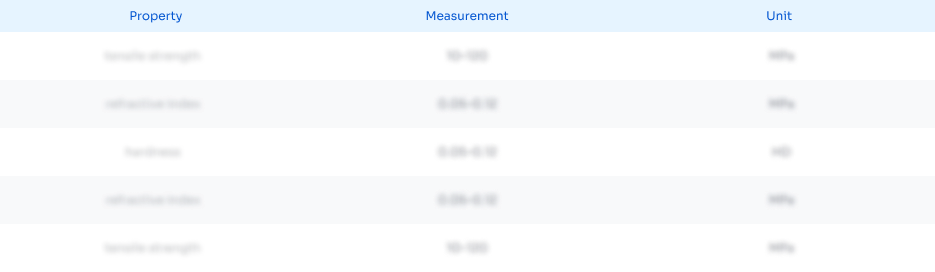
Abstract
Description
Claims
Application Information

- R&D
- Intellectual Property
- Life Sciences
- Materials
- Tech Scout
- Unparalleled Data Quality
- Higher Quality Content
- 60% Fewer Hallucinations
Browse by: Latest US Patents, China's latest patents, Technical Efficacy Thesaurus, Application Domain, Technology Topic, Popular Technical Reports.
© 2025 PatSnap. All rights reserved.Legal|Privacy policy|Modern Slavery Act Transparency Statement|Sitemap|About US| Contact US: help@patsnap.com