Slide palte deformed tooth stepless engagement adjustable gear
A technology of deformed teeth and slides, which is applied to gear transmissions, belts/chains/gears, V-shaped belts, etc., can solve the problems of low mechanical efficiency, narrow speed range, and low transmission power, and achieve low machining accuracy. Effect
- Summary
- Abstract
- Description
- Claims
- Application Information
AI Technical Summary
Problems solved by technology
Method used
Image
Examples
Embodiment Construction
[0109] Cylindrical movable gear continuously variable transmission series
[0110] Figure 1. Structural diagram of cylindrical live gear continuously variable transmission figure 2 , Structural diagram of cylindrical movable gear
[0111] image 3 , Structural Diagram of Cylindrical Live Gear Wheel Figure 4, Structural Diagram of Sliding Plate for Cylindrical Live Gear
[0112] Figure 5, Internal structure diagram of cylindrical movable gear Fig. 6, Plan view of internal structure of cylindrical movable gear
[0113] As shown in the figure: the input shaft is connected to the cogged wheel, and the movable gear is connected to the output shaft through a guide key or a spline, which can freely move axially while transmitting torque, and the meshing radius with the cogged wheel can be changed steplessly. Stepless speed change (in Fig. 1: A, B, C represent respectively: forward gear zone, reverse gear zone, neutral gear zone).
[0114] The structure of the cylindrical liv...
PUM
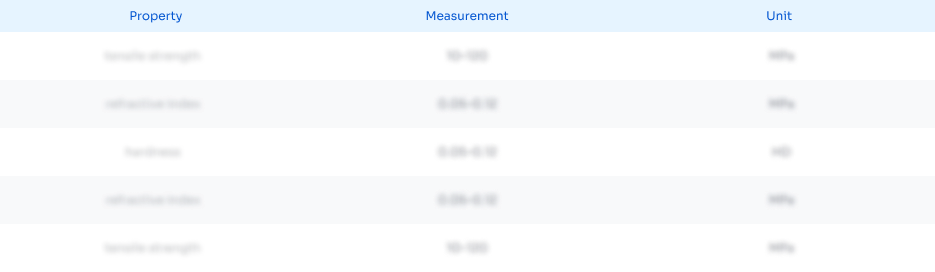
Abstract
Description
Claims
Application Information

- R&D
- Intellectual Property
- Life Sciences
- Materials
- Tech Scout
- Unparalleled Data Quality
- Higher Quality Content
- 60% Fewer Hallucinations
Browse by: Latest US Patents, China's latest patents, Technical Efficacy Thesaurus, Application Domain, Technology Topic, Popular Technical Reports.
© 2025 PatSnap. All rights reserved.Legal|Privacy policy|Modern Slavery Act Transparency Statement|Sitemap|About US| Contact US: help@patsnap.com