Method and apparatus employing integrated metrology for improved dielectric etch efficiency
A technology of equipment and measurement values, applied in semiconductor/solid state device testing/measurement, circuits, electrical components, etc., to solve the problem of inability to monitor wafer etching uniformity by interferometric sensors, interferometric sensors that cannot be monitored or corrected, and improper chip etching And other issues
- Summary
- Abstract
- Description
- Claims
- Application Information
AI Technical Summary
Problems solved by technology
Method used
Image
Examples
Embodiment Construction
[0040] The traditional measurement method for detecting the features formed on the surface of the semiconductor wafer during the manufacturing process cannot effectively analyze the error between the CD and / or the outline and the design rules, so as to provide early information for positively identifying the source of the defect, or to carry out the process control to reduce size variation. The present invention solves the CD control problem by reducing the CD variation by feeding back information about the CD and profile of the photoresist mask, and measuring the thickness of the underlying layer at multiple points on the wafer to adjust the next process of the inspected wafer ( such as etching process). In some embodiments of the present invention, CD, profile and thickness measurement, etch processing and post-etch cleaning are performed in a single module in a controlled environment, thereby increasing throughput and improving yield. The present invention provides a self-...
PUM
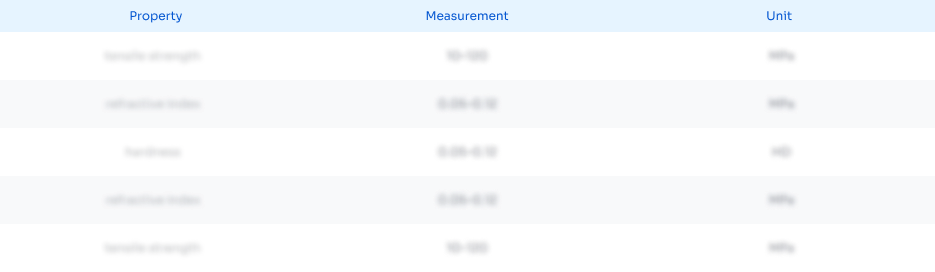
Abstract
Description
Claims
Application Information

- R&D Engineer
- R&D Manager
- IP Professional
- Industry Leading Data Capabilities
- Powerful AI technology
- Patent DNA Extraction
Browse by: Latest US Patents, China's latest patents, Technical Efficacy Thesaurus, Application Domain, Technology Topic, Popular Technical Reports.
© 2024 PatSnap. All rights reserved.Legal|Privacy policy|Modern Slavery Act Transparency Statement|Sitemap|About US| Contact US: help@patsnap.com