Amino sulfonic acid water reducing agent with very low alkali content and its production process
A technology of ultra-low alkali sulfamic acid and water reducing agent, applied in the field of building materials, can solve the problems of concrete threat, impact on concrete durability, deterioration of concrete structures, etc.
- Summary
- Abstract
- Description
- Claims
- Application Information
AI Technical Summary
Problems solved by technology
Method used
Examples
Embodiment 1
[0019] 1. The raw materials and formula (unit-Kg) of the present embodiment
[0020] p-Sulfuran: 225 kg;
[0021] Phenol: 84 kg;
[0022] Compounds containing amide groups (dicyandiamide and urea mixture, mass ratio is 1:3): 28 kg
[0023] Cresol: 12 kg;
[0024] Formaldehyde (37% content): 252 kg;
[0025] Alkaline regulator: calcium hydroxide: 14.8 kg; ammonia water: 34 kg
[0026] Water: 350.2 kg.
[0027] 2. Process steps and process parameters:
[0028] The preparation process of the present invention includes three steps: methylolation under alkaline conditions, alkaline condensation, and alkaline reforming steps, and each process step is carried out under normal pressure.
[0029] (1) Hydroxymethylation: 225 kg of p-aminobenzenesulfonic acid, 84 kg of phenol, 12 kg of cresol and 350.2 kg of water were added to the reactor, and after stirring evenly, 14.8 kg of calcium hydroxide was used to adjust the pH of the reaction system The value was adjusted to 8.0, 252 kg...
Embodiment 2
[0033] 1. The raw material of embodiment and formula (unit-Kg)
[0034] p-Sulfuran: 242 kg;
[0035] Phenol: 125 kg;
[0036] Melamine: 5.0 kg
[0037] Paraformaldehyde: 85 kg;
[0038] Alkaline regulator: calcium hydroxide 9.5 kg; ethanolamine: 45 kg
[0039] Water: 488.5 kg.
[0040] 2. Process steps and process parameters:
[0041] The preparation process of the present invention includes three steps: methylolation under alkaline conditions, alkaline condensation, and alkaline reforming steps, and each process step is carried out under normal pressure.
[0042] (1) Hydroxymethylation: 242 kg of p-aminobenzenesulfonic acid, 125 kg of phenol and 488.5 kg of water were added to the reactor, and after stirring evenly, the pH value of the reaction system was adjusted with 9.5 kg of calcium hydroxide and 15 kg of ethanolamine. Adjust to 8.5, add 85kg of paraformaldehyde dropwise within 0.5h, heat up to 50°C, and react for 3.0h.
[0043] (2) Alkaline condensation: the pH va...
Embodiment 3
[0046] 1. The raw material of embodiment and formula (unit-Kg)
[0047] 4-amino-1,3-phenyldisulfonic acid: 18 kg;
[0048] p-Sulfuran: 224 kg;
[0049] Phenol: 83 kg;
[0050] Urea: 16.5 kg
[0051] Bisphenol A: 12 kg;
[0052] Formaldehyde (37% content): 210 kg;
[0053] Alkaline regulator: ammonia water: 19.5 kg; diethanolamine: 48 kg
[0054] Water: 369 kg.
[0055] 1. Process steps and process parameters:
[0056] The preparation process of the present invention includes three steps: methylolation under alkaline conditions, alkaline condensation, and alkaline reforming steps, and each process step is carried out under normal pressure.
[0057] (1) Hydroxymethylation: Add 224 kg of p-aminobenzenesulfonic acid and 18 kg of 4-amino-1,3-phenyldisulfonic acid, 83 kg of phenol, 12 kg of bisphenol A and 369 kg of water into the reactor After stirring evenly, adjust the pH value of the reaction system to 7.5 with 16.5 kg of ammonia water, add 210 kg of formaldehyde dropwis...
PUM
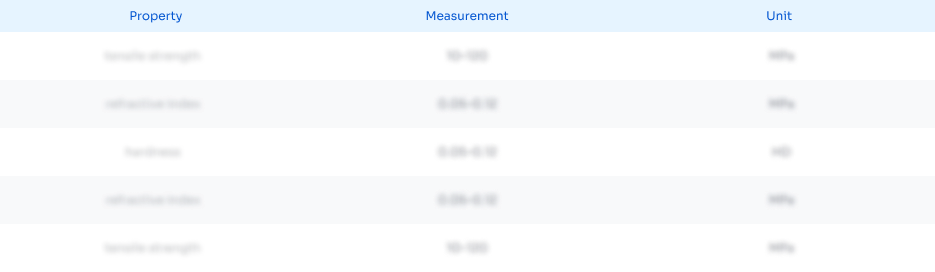
Abstract
Description
Claims
Application Information

- Generate Ideas
- Intellectual Property
- Life Sciences
- Materials
- Tech Scout
- Unparalleled Data Quality
- Higher Quality Content
- 60% Fewer Hallucinations
Browse by: Latest US Patents, China's latest patents, Technical Efficacy Thesaurus, Application Domain, Technology Topic, Popular Technical Reports.
© 2025 PatSnap. All rights reserved.Legal|Privacy policy|Modern Slavery Act Transparency Statement|Sitemap|About US| Contact US: help@patsnap.com