Method of improving surface cohesion performance of relative molecular weight polyethylene
A technology of molecular weight polyethylene and ultra-high molecular weight, which is applied in stretch spinning, filament forming treatment, textiles and papermaking, etc. It can solve the problems of fiber strength decline, fiber mechanical performance decline, and the difficulty of mastering the best process conditions. , to achieve the effect of maintaining strength and improving the bonding performance of the fiber surface
- Summary
- Abstract
- Description
- Claims
- Application Information
AI Technical Summary
Problems solved by technology
Method used
Examples
Embodiment 1
[0025] Vinyl acetate (VA) content is 28%, the ethylene-vinyl acetate copolymer (EVA) of melt index 190 is dissolved in xylene, makes composite extraction agent, and the massfraction of EVA in composite extraction agent is 0.1%, The ultra-high relative molecular weight polyethylene (UHMWPE) jelly fiber with a weight-average relative molecular weight of 1 million is extracted in a composite extractant for 10 minutes at 0.4 atmospheric pressure and a temperature of 80° C., and then dried at room temperature. The dry jelly fiber is stretched 20 times at 100°C for the first stage, 2 times for the second stage at 110°C, and 1.2 times for the third stage at 120°C to make the surface bonding performance better. Enhanced UHMWPE fibers.
Embodiment 2
[0027] Vinyl acetate (VA) content is 28%, the ethylene-vinyl acetate copolymer (EVA) of melt index 190 is dissolved in xylene, makes composite extraction agent, and the massfraction of EVA in composite extraction agent is 10%, The ultra-high relative molecular weight polyethylene (UHMWPE) jelly fiber with a weight-average relative molecular weight of 5 million is extracted in a composite extractant for 0.1 minute at 5 atmospheres at a temperature of 10° C., and then dried at room temperature. The dry jelly fiber is stretched 20 times at 100°C for the first stage, 2 times for the second stage at 110°C, and 1.2 times for the third stage at 120°C to make the surface bonding performance better. Enhanced UHMWPE fibers.
Embodiment 3
[0029] An ethylene-ethylene glycol copolymer with an ethylene glycol content of 18% is dissolved in xylene to make a composite extractant, and the mass fraction of the ethylene-ethylene glycol copolymer in the composite extractant is 3%. The ultra-high relative molecular weight polyethylene (UHMWPE) jelly fiber with a weight-average relative molecular weight of 3 million is extracted in a composite extractant for 0.1 minute at 5 atmospheres and at a temperature of 0° C., and then dried at room temperature. The dry jelly fiber is stretched 20 times at 100°C for the first stage, 2 times for the second stage at 110°C, and 1.2 times for the third stage at 120°C to make the surface bonding performance better. Enhanced UHMWPE fibers.
PUM
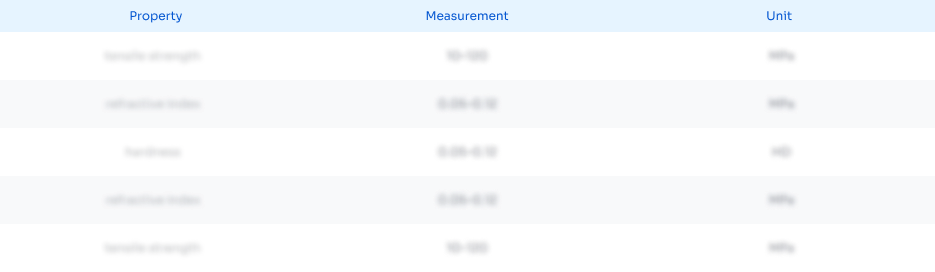
Abstract
Description
Claims
Application Information

- R&D
- Intellectual Property
- Life Sciences
- Materials
- Tech Scout
- Unparalleled Data Quality
- Higher Quality Content
- 60% Fewer Hallucinations
Browse by: Latest US Patents, China's latest patents, Technical Efficacy Thesaurus, Application Domain, Technology Topic, Popular Technical Reports.
© 2025 PatSnap. All rights reserved.Legal|Privacy policy|Modern Slavery Act Transparency Statement|Sitemap|About US| Contact US: help@patsnap.com