Technique for producing bulbs
A production process and technology for light bulbs, applied in electrical components and other directions, can solve problems such as exhaust rod crushing, filament curling, affecting the quality of light bulbs, etc.
- Summary
- Abstract
- Description
- Claims
- Application Information
AI Technical Summary
Problems solved by technology
Method used
Image
Examples
Embodiment Construction
[0021] The invention relates to a production process of a light bulb, which includes making a stem, threading, sealing, exhausting, and baking. The invention is an innovation and improvement of the production process from stem manufacturing to baking in the production process of ordinary lighting bulbs.
[0022] 1. The production process of the core column is: automatically lowering the horn, automatically loading two guide wires, automatically lowering the exhaust rod, flame heating, flattening, blowing low-pressure air into the exhaust rod and horn tube, and blowing in the second time Low-pressure air, natural cooling, automatic removal of the stem, and annealing in the annealing furnace. In the automatic lower exhaust rod 1, after the glass exhaust rod 1 is cut, the natural pressing method is adopted to remove the manipulator in the traditional process, and the split wire 2 jaws and horn 3 jaws in the special equipment for producing stem 6 The distance between the jaws of t...
PUM
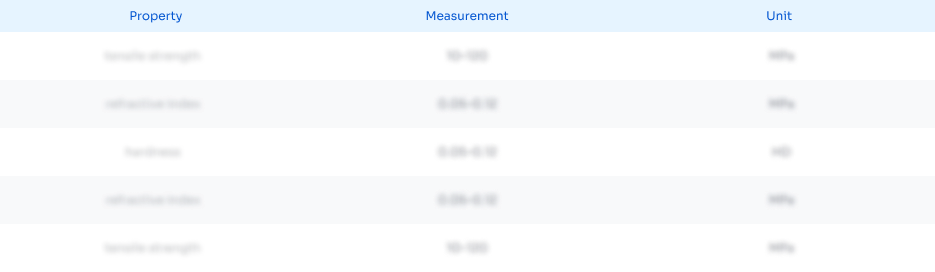
Abstract
Description
Claims
Application Information

- R&D Engineer
- R&D Manager
- IP Professional
- Industry Leading Data Capabilities
- Powerful AI technology
- Patent DNA Extraction
Browse by: Latest US Patents, China's latest patents, Technical Efficacy Thesaurus, Application Domain, Technology Topic, Popular Technical Reports.
© 2024 PatSnap. All rights reserved.Legal|Privacy policy|Modern Slavery Act Transparency Statement|Sitemap|About US| Contact US: help@patsnap.com