Production of clean high carbon chromic bearing steel
A technology of high-carbon chromium bearing steel and production method, which is applied in the field of smelting and production of high-carbon chromium bearing steel, and can solve the problem of instability in the smelting and production process of ultra-pure high-carbon chromium bearing steel, damage to the chemical balance of steel slag, and no nitrogen content involved, etc. problems, to achieve the effects of strong equipment and process versatility, increased smelting success rate, and low smelting production costs
- Summary
- Abstract
- Description
- Claims
- Application Information
AI Technical Summary
Problems solved by technology
Method used
Examples
Embodiment Construction
[0034] specific implementation plan
[0035] A steel company implements the patented method of the present invention and adopts a five-step smelting process: electric furnace batching optimization-→30 tons and 100 tons of electric arc furnace initial steelmaking molten steel-→bottom-blown argon ladle furnace refining of corresponding capacity-→corresponding capacity Vacuum furnace degassing-→die casting production line, successfully produced RSAE52100SF high-clean high-carbon chromium bearing steel (oxygen content ≤0.0007%, titanium content ≤0.0011%, nitrogen content ≤0.0055%, sulfur content ≤0.005%). In the first step, low-titanium, low-copper and low-phosphorus steel scrap and direct reduced iron are selected as ingredients: 55-60% of clean steel scrap, 10-15% of direct reduced iron, and 25-30% of high-quality pig iron. The second step is to dephosphorize and remove titanium in a 30-ton / 100-ton EBT electric furnace, remove the phosphorus content in the steel to ≤0.007%, and ...
PUM
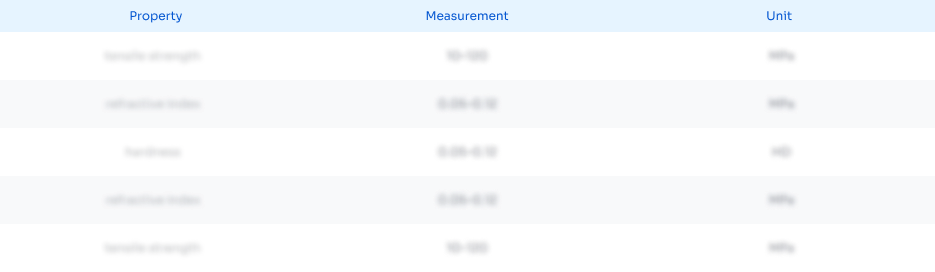
Abstract
Description
Claims
Application Information

- R&D
- Intellectual Property
- Life Sciences
- Materials
- Tech Scout
- Unparalleled Data Quality
- Higher Quality Content
- 60% Fewer Hallucinations
Browse by: Latest US Patents, China's latest patents, Technical Efficacy Thesaurus, Application Domain, Technology Topic, Popular Technical Reports.
© 2025 PatSnap. All rights reserved.Legal|Privacy policy|Modern Slavery Act Transparency Statement|Sitemap|About US| Contact US: help@patsnap.com