Coating for centrifugal casting high alloy furnace tube metal mould and method thereof
An alloy furnace tube and centrifugal casting technology, which is applied in the direction of casting molding equipment, molds, and mold components, can solve problems such as volume expansion, poor surface quality of furnace tubes, and sand sticking on the surface of furnace tubes, and achieve improved erosion resistance ability, improve surface quality, and reduce production costs
- Summary
- Abstract
- Description
- Claims
- Application Information
AI Technical Summary
Problems solved by technology
Method used
Examples
example 1
[0024] Example 1, zircon powder 100KG, silica sol 5KG, fluorite powder 2KG, cellulose 80G, polyvinyl alcohol 80G
[0025] Bentonite 3KG.
[0026] Mixing method: Add zircon powder, fluorite powder, and bentonite into the wheel mill, dry mix for 15 minutes, add 80G cellulose dissolved in water, 80G polyvinyl alcohol and 5KG water, and mix for 3 hours. Add 5KG of silica sol and mix and grind for 30 minutes.
[0027] The paint mixed by this method is off-white, paste-like paint with a delicate feel. In the process of use, it has the characteristics of moderate high-temperature strength and incrustation, and is suitable for the requirements of the centrifugal casting process of high-alloy vinyl pipes with small diameters.
example 2
[0028] Example 2, zircon powder 100KG, silica sol 8KG, fluorite powder 3KG, cellulose 150G, polyvinyl alcohol 100G
[0029] Bentonite 3KG.
[0030] Mixing method: with example 1. It is suitable for the centrifugal casting process requirements of high-alloy furnace tubes such as conversion tubes and manifolds with a diameter of 100-200mm.
example 3
[0031] Example 3, zircon powder 100KG, silica sol 15KG, fluorite powder 8KG, cellulose 200G, polyvinyl alcohol 200G
[0032] Bentonite 3KG.
[0033] Mixing method: with example 1. It is suitable for the requirements of the centrifugal casting process of high alloy furnace tubes such as manifolds, support rods and metallurgical reactors with a diameter greater than 200mm.
[0034] The above-mentioned mixing equipment uses a wheel-rolling paint mixing machine, and its model is CMSA-800 wheel-rolling machine, which is produced by Xiongyue Foundry in Gaizhou City, China.
[0035] The material has heat resistance, erosion resistance, low cost, good peeling performance, low temperature requirements for the mold cylinder during spraying, and low surface roughness of the furnace tube produced during use. It is suitable for petrochemical, metallurgy, building materials and other industries. Production of heat-resistant furnace tubes.
PUM
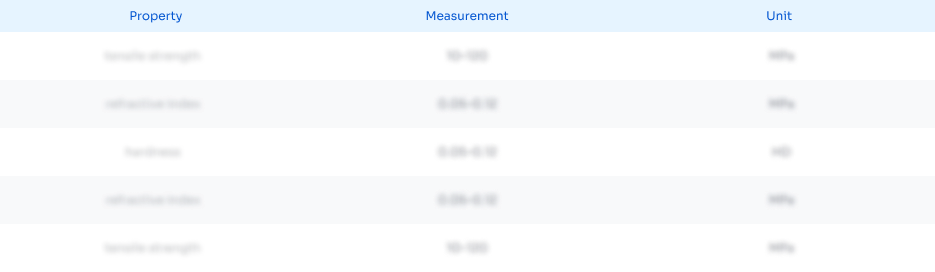
Abstract
Description
Claims
Application Information

- R&D
- Intellectual Property
- Life Sciences
- Materials
- Tech Scout
- Unparalleled Data Quality
- Higher Quality Content
- 60% Fewer Hallucinations
Browse by: Latest US Patents, China's latest patents, Technical Efficacy Thesaurus, Application Domain, Technology Topic, Popular Technical Reports.
© 2025 PatSnap. All rights reserved.Legal|Privacy policy|Modern Slavery Act Transparency Statement|Sitemap|About US| Contact US: help@patsnap.com