Organic sillicon modified acrylic ester/inorganic nano composite emulsion and its preparation
An acrylate and inorganic nano technology, which is applied in the field of organosilicon modified acrylate/inorganic nano composite emulsion and its preparation, can solve the problems of cumbersome operation process, limited improvement of coating performance and high production cost, and achieves enhanced interaction, Excellent tensile strength and improved stability
- Summary
- Abstract
- Description
- Claims
- Application Information
AI Technical Summary
Problems solved by technology
Method used
Examples
Embodiment 1
[0025] Weigh nano-SiO with an average particle size of 15nm 2 1.0g was added to 0.1g potassium persulfate, 0.5g OP-10, 5g 10% H 2 o 2 solution, in a mixed solution composed of 5g of 10% NaOH solution, stirred at high speed for 2 hours, added 2g of methacrylic acid, and stirred for 30. minutes. Add 43g of methyl methacrylate, stir evenly, prepare an inverse emulsion system, heat up to 65°C for inverse emulsion polymerization, react for 6 hours and then cool to 40°C, add 2g of sodium lauryl sulfate to the system, A mixed solution composed of 0.5g sodium carbonate, 5.5g OP-10 and 140g water was stirred at high speed for reverse phase, then added 52g butyl acrylate, 2g KH570, emulsified for 30 minutes, heated to 75°C, added 0.4g potassium persulfate Initiator dissolved in 10g of water, initiate the reaction, carry out conventional emulsion polymerization, heat preservation reaction for 3 hours, cool down to room temperature, neutralize with 1:1 (volume ratio) ammonia water, fil...
Embodiment 2
[0027] Weigh nano-TiO with an average particle size of 40nm 2 1.0g was added to 0.1g potassium persulfate, 0.5g OP-10, 5g 10% H 2 o 2 Solution, in a mixed solution composed of 5g of 10% NaOH solution, stir at high speed for 2 hours, let it stand overnight, add 2g of hydroxyethyl methacrylate, stir for 30 minutes, add 43g of methyl methacrylate, stir evenly, and prepare a reverse phase Emulsion system. The temperature was raised to 65° C., and 2 g of 1% sodium formaldehyde sulfoxylate solution was added to initiate the reaction to carry out inverse emulsion polymerization. After reacting for 6 hours, cool to 40°C, add a mixed solution consisting of 2g sodium lauryl sulfate, 0.5g sodium carbonate, 5.5g OP-10 and 140g water to the system, stir at high speed for reverse phase, and then add 52g of butyl acrylate and 5g of macromolecular silicon monomer containing double bonds were emulsified for 30 minutes. Raise the temperature to 75°C, add an initiator composed of 0.4g potas...
PUM
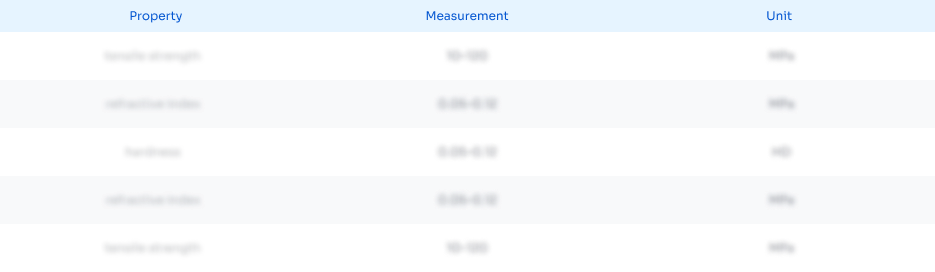
Abstract
Description
Claims
Application Information

- R&D
- Intellectual Property
- Life Sciences
- Materials
- Tech Scout
- Unparalleled Data Quality
- Higher Quality Content
- 60% Fewer Hallucinations
Browse by: Latest US Patents, China's latest patents, Technical Efficacy Thesaurus, Application Domain, Technology Topic, Popular Technical Reports.
© 2025 PatSnap. All rights reserved.Legal|Privacy policy|Modern Slavery Act Transparency Statement|Sitemap|About US| Contact US: help@patsnap.com