Manufacturing method of bimetal electroslag founding antiwear hopper teeth set
A technology of electroslag casting and manufacturing method, which is used in earthmovers/shovels, construction, etc., can solve the problems of difficult quality control, many influencing factors, large machining allowance, etc., and achieves stable casting process and slag layer thickness. The effect of convenience and high material utilization
- Summary
- Abstract
- Description
- Claims
- Application Information
AI Technical Summary
Problems solved by technology
Method used
Image
Examples
Embodiment Construction
[0025] As shown in Figure 1 and Figure 2, the first embodiment is suitable for the manufacture of larger bucket teeth. The bucket teeth are composed of two materials. The shape of the bucket teeth is wedge-shaped. Parallel straight planes, the tooth shank 2 is made of low carbon alloy steel or manganese steel, and the tooth tip is made of high chromium cast iron. The side of the prepared tooth shank 2 is erected as the base surface, and it is stacked from bottom to top like a wall. One end of the open-type copper water-cooled crystallizer 4 is close to the working surface of the tooth handle 2, and an insulating plate 5 is added between the two. The casting cavity 6 of the tip of the tooth tip is initially installed with not less than three tooth shanks and three groups of molds, and then the consumable electrode 1 made of high-chromium cast iron is used for electroslag casting of the tip of the tooth, and the electroslag is used for electroslag casting of the tip of the tooth....
PUM
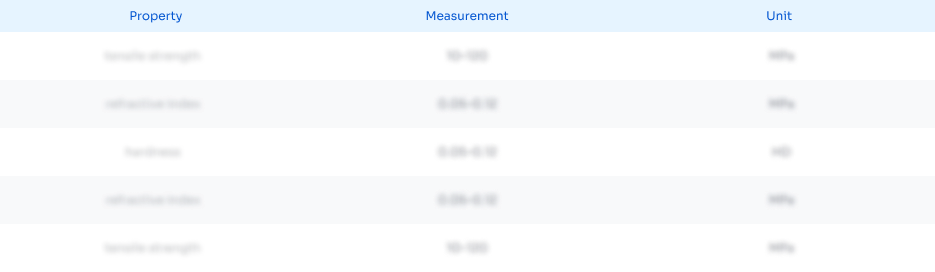
Abstract
Description
Claims
Application Information

- Generate Ideas
- Intellectual Property
- Life Sciences
- Materials
- Tech Scout
- Unparalleled Data Quality
- Higher Quality Content
- 60% Fewer Hallucinations
Browse by: Latest US Patents, China's latest patents, Technical Efficacy Thesaurus, Application Domain, Technology Topic, Popular Technical Reports.
© 2025 PatSnap. All rights reserved.Legal|Privacy policy|Modern Slavery Act Transparency Statement|Sitemap|About US| Contact US: help@patsnap.com