High-current density electronic emission body rareearth-Sc-W based material and mfg. method thereof
An electron emitter and high current density technology, applied in the directions of discharge tube solid thermionic cathode, discharge tube main electrode, discharge tube cold cathode, etc., can solve problems such as uneven emission, affecting the improvement of cathode life, and difficulty in replenishment, etc. Achieve the effect of improving high temperature resistance, improving uniformity and good repeatability
- Summary
- Abstract
- Description
- Claims
- Application Information
AI Technical Summary
Problems solved by technology
Method used
Image
Examples
example 1
[0020] Example 1, 10.05 grams of scandium nitrate was dissolved in water, and added to 120.64 grams of powdered blue tungsten (wherein scandium oxide accounted for 3% of the total weight of the final product rare earth scandium tungsten-based high current density electron emitter material), in a multi-stage hydrogen furnace In the process, reduce at 650°C for 1 hour, and reduce at 900°C for 2 hours to obtain tungsten powder doped with scandium oxide; press the above-mentioned tungsten powder doped with scandium oxide on a hydraulic press to form a thin slice sample of Φ3.5×1mm, and the pressing pressure is 350Mpa / cm 2 , in a tungsten wire mesh furnace, sintering in a hydrogen atmosphere at 1750 ° C to prepare a rare earth scandium tungsten sintered body. The above-mentioned sintered body is impregnated with aluminate, ultrasonically cleaned and annealed, and then laser-welded with a molybdenum sleeve to produce an electron emitter material.
example 2
[0021] Example 2, 10.05 grams of scandium nitrate and 1.441 grams of ammonium rhenate were dissolved in water respectively and added to 119.39 grams of powdered blue tungsten (wherein scandium oxide accounts for the total weight of the final product rare earth scandium tungsten-based high current density electron emitter material 3%, rhenium accounted for 1%), in a multi-stage hydrogen furnace, 500 ° C reduction for 1 hour, 800 ° C reduction for 3 hours, to obtain powder doped with scandium oxide and rhenium; press the above tungsten powder on a hydraulic press to Φ3. 5×1mm thin slice sample, the pressing pressure is 350Mpa / cm 2 , in a tungsten wire mesh furnace, sintering in a hydrogen atmosphere at 1400 ° C to prepare a rare earth scandium tungsten sintered body. The above-mentioned sintered body is impregnated with aluminate, ultrasonically cleaned and annealed, and then laser-welded with a molybdenum sleeve to produce an electron emitter material.
example 3
[0022] Example 3, 33.50 grams of scandium nitrate and 4.323 grams of ammonium rhenate were dissolved in water respectively and added to 108.20 grams of powdered blue tungsten (wherein scandium oxide accounts for the total weight of the final product rare earth scandium tungsten-based high current density electron emitter material 10% of rhenium, rhenium accounted for 3%), in a multi-stage hydrogen furnace, 650 ℃ reduction for 1.5 hours, 900 ℃ reduction for 2 hours, get doped scandium oxide and rhenium, the tungsten powder is pressed on the hydraulic press to Φ3.5 For a thin sheet sample of ×1mm, the pressing pressure is 350Mpa / cm 2 , in a tungsten wire mesh furnace, sintering in a hydrogen atmosphere at 1400 ° C to prepare a rare earth scandium tungsten sintered body. The above-mentioned sintered body is impregnated with aluminate, ultrasonically cleaned and annealed, and then laser-welded with a molybdenum sleeve to produce an electron emitter material.
PUM
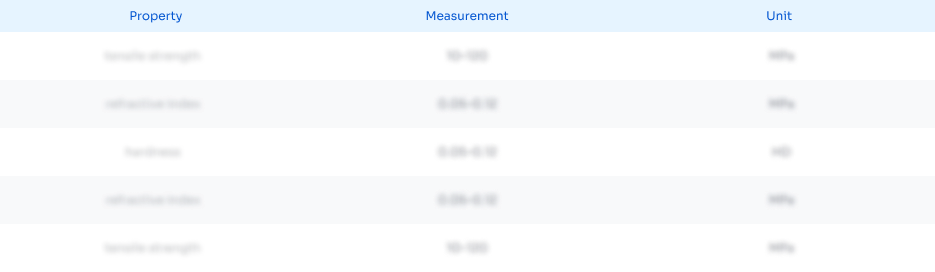
Abstract
Description
Claims
Application Information

- R&D Engineer
- R&D Manager
- IP Professional
- Industry Leading Data Capabilities
- Powerful AI technology
- Patent DNA Extraction
Browse by: Latest US Patents, China's latest patents, Technical Efficacy Thesaurus, Application Domain, Technology Topic, Popular Technical Reports.
© 2024 PatSnap. All rights reserved.Legal|Privacy policy|Modern Slavery Act Transparency Statement|Sitemap|About US| Contact US: help@patsnap.com