Reformed oil olefine saturation hydrogenation method
A technology for reforming oil and oil olefins, which is applied in the field of saturated hydrogenation of olefins. It can solve the problem that the bromine price cannot meet the product quality requirements, and achieve the effects of low metal content, high low-temperature activity, and reduced energy consumption.
- Summary
- Abstract
- Description
- Claims
- Application Information
AI Technical Summary
Problems solved by technology
Method used
Examples
preparation example Construction
[0033] The preferred preparation method of the catalyst comprises impregnating the alumina support with an aqueous solution containing molybdenum and / or tungsten compounds and nickel compounds and an aqueous solution containing cobalt compounds, and calcining the alumina support impregnated with molybdenum and / or tungsten, nickel and cobalt, Wherein, the process of impregnating the alumina carrier with an aqueous solution of a cobalt-containing compound is carried out separately from the process of impregnating the alumina carrier with an aqueous solution of a tungsten and / or molybdenum compound and a nickel compound, and the impregnation of the alumina carrier with an aqueous solution of a cobalt-containing compound The process of carrier is after the alumina carrier is impregnated with the aqueous solution containing molybdenum and / or tungsten compound and nickel compound and calcined. more than 1 hour. Using this method can further improve the low-temperature activity of th...
example 1
[0049] This example illustrates the preparation of a support for the catalyst used in the process provided by the invention.
[0050] Take by weighing 5000 grams of aluminum hydroxide powder A (solid content is 70% by weight, pseudo-boehmite content is 85% by weight, produced by Shandong Aluminum Factory) and mixed with an appropriate amount of water, extruded into a circle with a circumscribed diameter of 1.6 mm. The trefoil strips were dried at 120°C for 2 hours, fired at 600°C for 4 hours, and the length of the obtained trefoil strips was cut into 2-3 mm to obtain the carrier Z 1 . Carrier Z 1 The specific surface area and pore volume are listed in Table 1. The specific surface and pore volume were measured by low-temperature nitrogen adsorption BET method (the same below).
example 2
[0052] This example illustrates the preparation of a support for the catalyst used in the process provided by the invention.
[0053] Take by weighing 500 grams of aluminum hydroxide powder A described in Example 1 (70 weight percent of solid content, 85 weight percent of pseudo-boehmite content, produced by Shandong Aluminum Works) and 500 grams of aluminum hydroxide powder B (70 weight percent of solid content, Pseudo-boehmite content 70% by weight, produced by Changling Oil Refinery Catalyst Factory), fully mixed, added appropriate amount of water to mix evenly, extruded into a trefoil-shaped strip with a circumscribed circle diameter of 1.6 mm with an extruder, and dried at 120 ° C 2 hours, 600 ° C for 4 hours, cut the length of the obtained trefoil into 2-3 mm, and make the carrier Z 2 . Carrier Z 2 The specific surface area and pore volume are listed in Table 1.
PUM
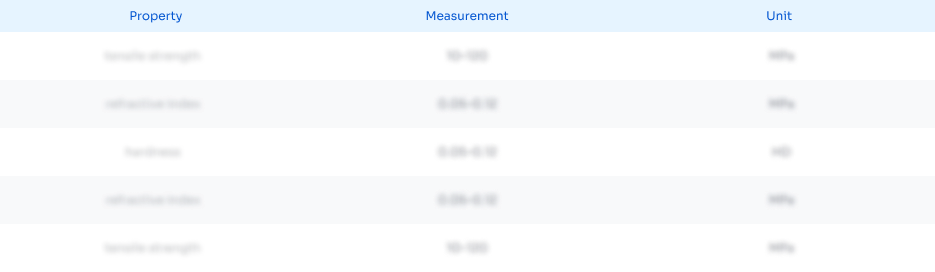
Abstract
Description
Claims
Application Information

- R&D
- Intellectual Property
- Life Sciences
- Materials
- Tech Scout
- Unparalleled Data Quality
- Higher Quality Content
- 60% Fewer Hallucinations
Browse by: Latest US Patents, China's latest patents, Technical Efficacy Thesaurus, Application Domain, Technology Topic, Popular Technical Reports.
© 2025 PatSnap. All rights reserved.Legal|Privacy policy|Modern Slavery Act Transparency Statement|Sitemap|About US| Contact US: help@patsnap.com