Hot dipping aluminium and aluminium alloy inactivation process of plating
A hot-dip aluminum and aluminum alloy technology, applied in hot-dip plating process, metal material coating process, coating and other directions, can solve the problems of high solvent price, toxic and expensive fluoride salt components, and achieve the process flow Simple, easy to operate, low cost effect
- Summary
- Abstract
- Description
- Claims
- Application Information
AI Technical Summary
Problems solved by technology
Method used
Examples
Embodiment 1
[0032] Embodiment 1. Carbon steel Q235, 760×13×1.5mm. With 20% NaOH and 0.5% Na 2 CO 3 The resulting solution was degreased at 90°C for 20 minutes. with 20%H 2 SO 4 Add a small amount of corrosion inhibitor solution, pickle at 70°C for 15 minutes, wash with water, soak in 3% dilute hydrochloric acid solution for 5 minutes, and wash with water. Immerse in a passivator solution (0.4% CrO 3 +0.1%K 2 MnO 4 +0.4%NaNO 2 + water), treated at room temperature for 2 min, washed with water, and dried. Preheat at 150°C for 15 minutes. Immerse in pure aluminum plating solution at 730°C for 5 minutes, lift out of the furnace at a speed of 6m / min, and cool in air to obtain a smooth, flat, seamless, and void-free aluminum coating. The total thickness of the coating is 132 μm, and the thickness of the intermediate alloy layer is 78 μm.
Embodiment 2
[0033] Embodiment 2. Iron casting, 80*35*5mm, its chemical composition is 3.24%C, 1.82%Si, 1.01%Mn, 0.06%P, 0.08%S, and the surface of the casting is treated by sandblasting. Oil was removed with 20% NaOH aqueous solution at 100°C for 15 min. with 25%H 2 SO 4 Add a small amount of corrosion inhibitor solution, pickle at 70°C for 10 minutes, wash with water, soak in 3% dilute hydrochloric acid solution for 5 minutes, and wash with water. With a passivating agent solution (2% CrO 3 +0.3%NaNO 2 + water), treated at room temperature for 3 minutes, and dried. Preheat at 160°C for 15 minutes, then immerse in pure aluminum plating solution at 760°C for 7 minutes, and lift the furnace at a speed of 4.5m / min. The total thickness of the coating is 116 μm, and the thickness of the intermediate alloy layer is 62 μm.
Embodiment 3
[0034] Example 3. Oil pipe steel 50Mn, φ60×5×110mm. Degreasing and pickling in the same manner as in Example 1. With a passivating agent solution (1.5% CrO 3 +0.2%K 2 MnO 4 + water), treated at room temperature for 1.5 min, washed with water, and dried. Preheat at 180°C for 20 minutes. Immerse in an aluminum-silicon alloy (containing 3% silicon) plating solution at 780°C and keep warm for 10 minutes, and the lifting speed out of the furnace is 7.5m / min. The resulting coating is bright and has no missing plating. The total thickness of the coating is 106 μm, and the thickness of the intermediate alloy layer is 53 μm.
PUM
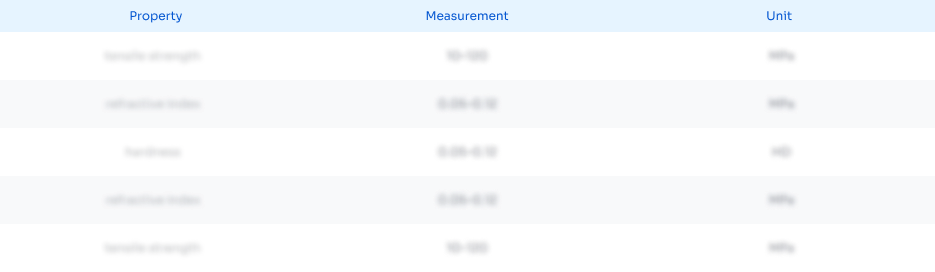
Abstract
Description
Claims
Application Information

- R&D Engineer
- R&D Manager
- IP Professional
- Industry Leading Data Capabilities
- Powerful AI technology
- Patent DNA Extraction
Browse by: Latest US Patents, China's latest patents, Technical Efficacy Thesaurus, Application Domain, Technology Topic, Popular Technical Reports.
© 2024 PatSnap. All rights reserved.Legal|Privacy policy|Modern Slavery Act Transparency Statement|Sitemap|About US| Contact US: help@patsnap.com