Method for providing a component of a large machine with a protective coating
A technology of machine components and protective layers, applied in the direction of engine components, machines/engines, valve devices, etc., to avoid internal stress, high stability, and time saving
- Summary
- Abstract
- Description
- Claims
- Application Information
AI Technical Summary
Problems solved by technology
Method used
Image
Examples
Embodiment Construction
[0016] The main field of application of the present invention is to configure a protective layer processed by overlay welding for large machines, such as components of two-stroke large diesel engines, wherein the protective layer to be coated has a rather heavy mass of at least 10 kg, for a two-stroke large diesel engine This is often the case with the exhaust valves or the protection of the piston crowns of large stroke diesel engines.
[0017] Figure 1 shows an exhaust valve 1 of a two-stroke large diesel engine. This can be, for example, a vent valve suitable for an 80 cm hole. On the underside 2 of its valve disk 3 facing the combustion chamber during operation, this exhaust valve is provided with a protective layer 4 , for example of a nickel alloy, which is applied by means of a welding device 5 in a build-up welding process. The welding device 5 can be a gas shielded welding device (GMAW) or an electroslag welding device (ESW).
[0018] The welding device 5 is equippe...
PUM
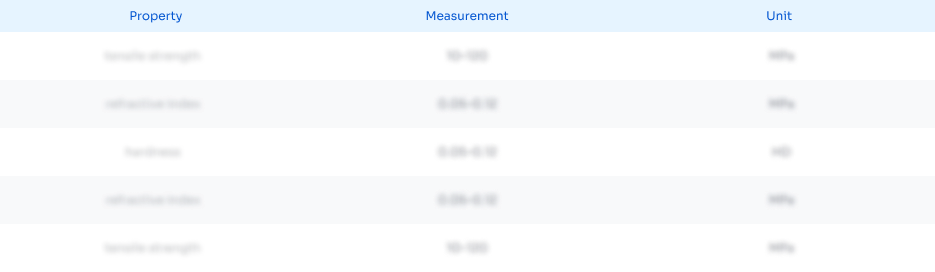
Abstract
Description
Claims
Application Information

- R&D Engineer
- R&D Manager
- IP Professional
- Industry Leading Data Capabilities
- Powerful AI technology
- Patent DNA Extraction
Browse by: Latest US Patents, China's latest patents, Technical Efficacy Thesaurus, Application Domain, Technology Topic, Popular Technical Reports.
© 2024 PatSnap. All rights reserved.Legal|Privacy policy|Modern Slavery Act Transparency Statement|Sitemap|About US| Contact US: help@patsnap.com