Method of preparing high-strength silicate wall material by utilizing chemical white sludge
A technology of wall materials and white mud slag, which is applied in the direction of solid waste management, sustainable waste treatment, climate sustainability, etc., can solve the problems of energy consumption increasing production costs, high dispersion, and product strength performance decline, etc., to achieve Reduced production costs, compact process layout, and electricity cost savings
- Summary
- Abstract
- Description
- Claims
- Application Information
AI Technical Summary
Problems solved by technology
Method used
Image
Examples
Embodiment 1
[0017] Example 1: Combining figure 1 , the first step: add 450kg of calcium carbide sludge containing water, 6.2kg of water reducer and 75kg of water into the mortar mixer, stir well and evenly, and the mixing time is 2 to 3 minutes. At this time, the white mud slag is plasticized into Uniform white mud slurry;
[0018] The second step: continue to add 450kg of fine yellow sand to the mixer, stir evenly, and stir for 2 to 3 minutes, and the mixing material obtained at this time is the base material;
[0019] The third step: add 450kg of fine yellow sand, 225kg of coarse aggregate and the base material obtained in the first step and the second step into another mixer at the same time, and stir for 2 to 3 minutes to prepare the mixture;
[0020] Step 4: The prepared mixture is molded into silicate adobe under a pressure of 18MPa.
[0021] Step 5: Carry out autoclaving curing of the formed silicate bricks, specifically heating up for 2 hours, constant temperature and pressure 1...
Embodiment 2
[0022] Example 2: Combining figure 2 , the first step: add 450kg of water-containing calcium carbide sludge into the mixer, fully stir evenly, and the stirring time is 2 to 3 minutes. At this time, the white mud slag is plasticized into a uniform white mud slag slurry;
[0023] The second step: continue to add 450kg of fine powder quartz to the mixer, stir evenly, and stir for 2 to 3 minutes, and the stirring material obtained at this time is the base material;
[0024] The third step: add 400kg of fine powder quartz, 375kg of coarse aggregate and the base material obtained in the first step and the second step to another mixer at the same time, and stir for 2 to 3 minutes to prepare the mixture;
[0025] The fourth step: the prepared mixture is formed into silicate bricks under a pressure of 19MPa;
[0026] Step 5: The molded silicate adobe is autoclaved and cured. Specifically, the temperature is raised for 2 hours, the constant temperature pressure is 1Mpa, the constant t...
Embodiment 3
[0027] Example 3: Binding image 3 , the first step: precipitation and concentration, because the calcium carbide mud slag mixture is a suspension with a high water content, it should be precipitated and concentrated to reduce the water content first, and the white mud slag solid content of the concentrated suspension should be measured;
[0028] Step 2: In the concentrated and precipitated white mud slag slurry, the mass ratio of white mud slag to fly ash is 1:0.8, and stirred evenly, and then the solid-liquid separation is carried out through a filter press, and the obtained filter residue can be used as a mixture the base of the material;
[0029] Step 3: Add the metered white mud slag and filter residue of silicon material and the remaining fly ash and aggregate into the mixer to make the brick adobe mixture, wherein the mass ratio of base material, fly ash and aggregate It is 1:0.5:0.4.
[0030] Step 4: The prepared mixture is molded into silicate bricks under a pressur...
PUM
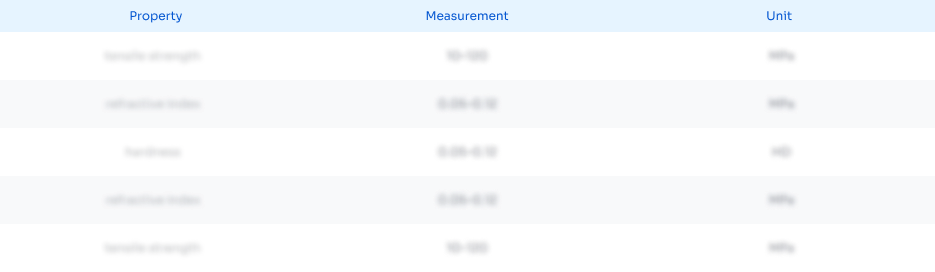
Abstract
Description
Claims
Application Information

- R&D
- Intellectual Property
- Life Sciences
- Materials
- Tech Scout
- Unparalleled Data Quality
- Higher Quality Content
- 60% Fewer Hallucinations
Browse by: Latest US Patents, China's latest patents, Technical Efficacy Thesaurus, Application Domain, Technology Topic, Popular Technical Reports.
© 2025 PatSnap. All rights reserved.Legal|Privacy policy|Modern Slavery Act Transparency Statement|Sitemap|About US| Contact US: help@patsnap.com