Fluoropolymer modified polyacrylate dispersion and its preparation and use
A polyacrylate emulsion and polymer technology, applied in the field of fluorine-containing polymer modified polyacrylate emulsion, can solve the problems of toxicity, poor compatibility of polyacrylic resin, etc., achieve simple production process, improve water resistance and Self-cleaning, overcoming expensive effects
- Summary
- Abstract
- Description
- Claims
- Application Information
AI Technical Summary
Problems solved by technology
Method used
Examples
Embodiment 1
[0028] Embodiment one, (mass percentage %)
[0029] Weigh 5% polytetrafluoroethylene micropowder in 45.7% water, add 1.0% fluorocarbon emulsifier, heat to 45°C for pre-emulsification for 1 hour, then add 0.4% sodium dodecylbenzenesulfonate, octylphenol polyoxyethylene 0.3% ether, add 15% water to the pre-emulsified polytetrafluoroethylene and pour it into a four-necked reaction flask equipped with a stirrer, a reflux condenser, and a constant temperature heating sensor, and stir for about 10 minutes. When the temperature reaches 40°C, Using the "semi-hungry drop method", first add 20% of 32% mixed monomers (including 12.8% butyl acrylate, 12.8% methyl methacrylate, and 6.0% styrene) at a rate of 1-2 drops per second. Continue heating, after the temperature reaches 70°C, add 25% of 0.3% ammonium persulfate dropwise at a rate of 4 drops per second, and continuously add 0.3% of pH regulator sodium bicarbonate, keep the temperature at 70°C, 2- The remaining mixed monomers and amm...
Embodiment 2
[0031] Weigh 3% polytetrafluoroethylene micropowder in 50% water, add 2% fluorocarbon emulsifier, heat at 50°C for pre-emulsification for 1 hour, then add 0.24% sodium dodecylbenzenesulfonate, octylphenol polyoxyethylene ether 0.46%, add 13.5% water to the pre-emulsified polytetrafluoroethylene and pour it into a four-necked reaction flask equipped with a stirrer, a reflux condenser, and a constant temperature heating sensor, and stir for about 30 minutes. When the temperature reaches 50°C, use "Semi-hungry drop method", first add 10% of 33% mixed monomer (including 18% butyl acrylate, 10% methyl methacrylate, and 5% styrene) at a drop rate of 1-2 drops per second, and continue Heating, after the temperature reaches 60°C, add 22% of 0.4% ammonium persulfate dropwise at a rate of 4 drops per second, 0.4% of the pH regulator sodium bicarbonate, keep the temperature at 75°C, drop the remaining monomer and Ammonium persulfate is cooled and discharged. After the emulsion is complet...
Embodiment 3
[0033] Weigh 1% polytetrafluoroethylene micropowder in 48.5% water, add 1.5% fluorocarbon emulsifier, heat at 60°C for pre-emulsification for 1 hour, then add 0.41% sodium dodecylbenzenesulfonate, octylphenol polyoxyethylene ether 0.29%, add 17.5% water to the pre-emulsified polytetrafluoroethylene and pour it into a four-necked reaction flask equipped with a stirrer, a reflux condenser, and a constant temperature heating sensor, and stir for about 10 minutes. When the temperature reaches 40°C, use "Semi-hungry drop method", first add 15% of 30% of mixed monomer (10% of butyl acrylate, 15% of methyl methacrylate, 5% of styrene) at a rate of 1-2 drops per second, Continue heating, after the temperature reaches 50°C, drop 25% of 0.3% ammonium persulfate at a rate of 4 drops per second, and 0.3% of the pH regulator sodium bicarbonate, keep the temperature at 80°C, and drop the remaining monomers in 2 hours And ammonium persulfate, cooling discharge, after the emulsion is complete...
PUM
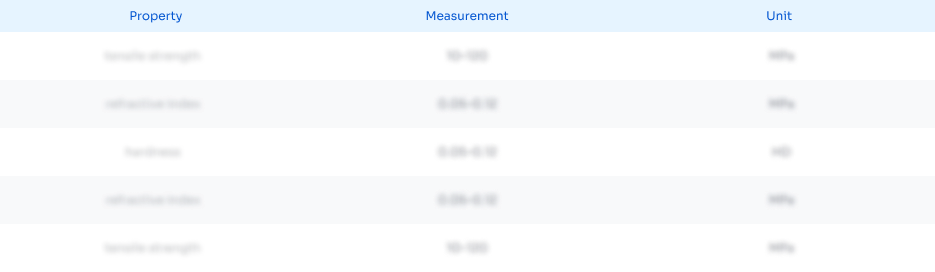
Abstract
Description
Claims
Application Information

- R&D
- Intellectual Property
- Life Sciences
- Materials
- Tech Scout
- Unparalleled Data Quality
- Higher Quality Content
- 60% Fewer Hallucinations
Browse by: Latest US Patents, China's latest patents, Technical Efficacy Thesaurus, Application Domain, Technology Topic, Popular Technical Reports.
© 2025 PatSnap. All rights reserved.Legal|Privacy policy|Modern Slavery Act Transparency Statement|Sitemap|About US| Contact US: help@patsnap.com