Die changing method and device for stamping processing multiple die of sheet material
A stamping processing and multi-mold technology, applied in metal processing equipment, forming tools, manufacturing tools, etc., can solve the problems of short service life, high cost, mold clamping error, etc., and achieve enhanced work stability, extended service life, and reduced The effect of device cost
- Summary
- Abstract
- Description
- Claims
- Application Information
AI Technical Summary
Problems solved by technology
Method used
Image
Examples
Embodiment Construction
[0014] The specific embodiments of the present invention will be described in further detail below in conjunction with the accompanying drawings:
[0015] As shown in the figure, the lower die frame 1 is fixed on the press base 13, and the upper die frame 10 is fixed on the hammer 9 of the press machine. With the center line 14 of the hammer 9 of the press as the axis, the lower die 2 of a plurality of dies arranged in the circumferential direction is fixed to the lower die frame 1 . The upper molds 5 of a plurality of molds corresponding to the arrangement positions of the lower molds 2 are installed on the upper mold base 10 . A rotary die changer 7 is provided above each upper die 5 in the upper die frame 10 , and the rotary die changer 7 is mounted on a fixed shaft 8 overlapping the centerline 14 of the hammer 9 of the press. A transmission gear set 11 is installed beside the rotary die changer 7 , and the output gear of the transmission gear set 11 directly meshes with t...
PUM
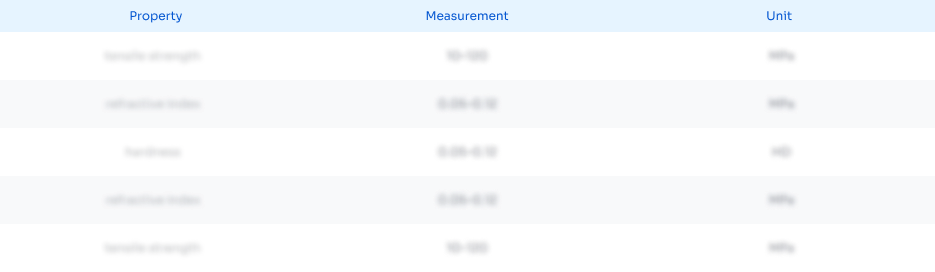
Abstract
Description
Claims
Application Information

- R&D
- Intellectual Property
- Life Sciences
- Materials
- Tech Scout
- Unparalleled Data Quality
- Higher Quality Content
- 60% Fewer Hallucinations
Browse by: Latest US Patents, China's latest patents, Technical Efficacy Thesaurus, Application Domain, Technology Topic, Popular Technical Reports.
© 2025 PatSnap. All rights reserved.Legal|Privacy policy|Modern Slavery Act Transparency Statement|Sitemap|About US| Contact US: help@patsnap.com