Adsorption pad for polishing glass display screen and preparation method thereof
A technology for a display screen and an adsorption pad, which is applied in grinding/polishing equipment, chemical instruments and methods, machine tools for surface polishing, etc. Short service life and other problems, to achieve the effect of long service life, reduced friction coefficient and cost saving
- Summary
- Abstract
- Description
- Claims
- Application Information
AI Technical Summary
Problems solved by technology
Method used
Image
Examples
Embodiment 1
[0035] The present embodiment provides a thermally conductive filler, which is made by the following steps:
[0036] Step A1, 0.35g graphene oxide and 100mL DMF were ultrasonically treated for 20min and then added 25mg didodecyldimethyl ammonium bromide, under nitrogen protection, stirred and reacted for 24h, then added 18mg 2-(7-azobenzo Triazole)-tetramethylurea hexafluorophosphate and 0.18g octa(aminophenyltrioxysilane), reacted at 78°C for 6h at constant temperature, filtered with suction, the filter cake was washed with ethanol for 3 times, and vacuum dried at 60°C 12h to obtain aminated nanoparticles;
[0037] Step A2: Mix 1.3g of aminated nanoparticles and 60mL of DMF, add 0.4g of 3-hydroxypropionyl chloride and 5mL of triethylamine, heat up to 90°C, react at constant temperature for 5h, suction filtration, and wash the filter cake with anhydrous ethanol 3 times Afterwards, it was vacuum-dried at 60° C. to constant weight to obtain a thermally conductive filler.
Embodiment 2
[0039] The present embodiment provides a thermally conductive filler, which is made by the following steps:
[0040] Step A1, 0.35g graphene oxide and 100mL DMF were ultrasonically treated for 20min and then added 25mg diddecyldimethyl ammonium bromide, under nitrogen protection, stirred and reacted for 24h, then added 20mg 2-(7-azobenzo triazole)-tetramethylurea hexafluorophosphate and 0.20g octa(aminophenyltrioxysilane), reacted at constant temperature for 6 hours at 78°C, filtered with suction, and washed the filter cake with ethanol for 5 times, and vacuum-dried at 60°C 12h to obtain aminated nanoparticles;
[0041] Step A2: Mix 2.0g of aminated nanoparticles and 60mL of DMF, add 0.6g of 3-hydroxypropionyl chloride and 5mL of triethylamine, heat up to 90°C, react at constant temperature for 5h, suction filtration, and wash the filter cake with anhydrous ethanol 3 times Then, vacuum-drying to constant weight at 60° C. to obtain a thermally conductive filler.
Embodiment 3
[0043] The present embodiment provides a protective agent, which is made by the following steps:
[0044] Step B1, add 50mmol of aniline, 0.1g of p-toluenesulfonic acid and 42.6mL of xylene to the three-necked flask, heat up to 100°C under stirring, then dropwise add 53mmol of hexafluoroacetone trihydrate, heat up to 130°C, and keep the reaction for 1h , cooled to room temperature and filtered, and the filter cake was recrystallized in toluene to obtain hydroxyfluoroaniline;
[0045] Step B2, under nitrogen protection, add 0.061mol 3-(3,5-di-tert-butyl-4-hydroxyphenyl) methyl propionate, 0.05mol hydroxyfluoroaniline and 250mL xylene into the three-necked flask, add zinc acetate , the absolute pressure was controlled at 22kPa, and the temperature was slowly raised to reflux for 5h under stirring. After the reaction was completed, it was cooled to room temperature and filtered. The filter cake was recrystallized in absolute ethanol to obtain esterified aniline. The consumption o...
PUM
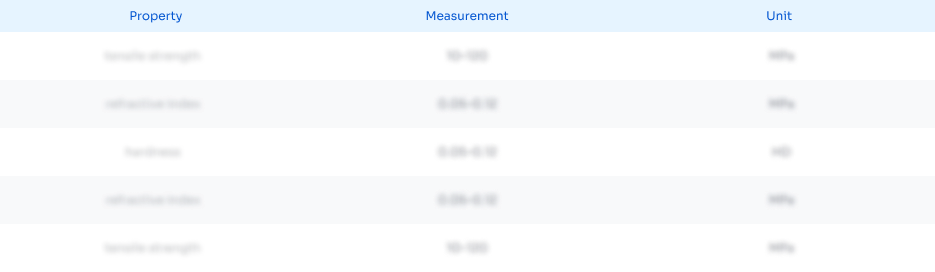
Abstract
Description
Claims
Application Information

- R&D
- Intellectual Property
- Life Sciences
- Materials
- Tech Scout
- Unparalleled Data Quality
- Higher Quality Content
- 60% Fewer Hallucinations
Browse by: Latest US Patents, China's latest patents, Technical Efficacy Thesaurus, Application Domain, Technology Topic, Popular Technical Reports.
© 2025 PatSnap. All rights reserved.Legal|Privacy policy|Modern Slavery Act Transparency Statement|Sitemap|About US| Contact US: help@patsnap.com