Preparation method of ultra-large aluminum alloy ring forge piece
A super-large ring, aluminum alloy technology, applied in metal processing equipment and other directions, can solve the problems of small anisotropy of mechanical properties of ring forgings, anisotropy of ring parts, etc., to reduce smelting defects, optimize structure, and improve alloy toughness. Effect
- Summary
- Abstract
- Description
- Claims
- Application Information
AI Technical Summary
Problems solved by technology
Method used
Image
Examples
Embodiment 1
[0042] This embodiment provides a preparation method of an aluminum alloy super-large ring forging, and the preparation method includes the following steps:
[0043] (1) Control the above-mentioned aluminum alloy (in terms of weight per hundred parts of aluminum alloy, composition: 0.1 part of Cu, 1.8 part of Mg, 5.0 part of Zn, 0.1 part of Ti, 0.2 part of Cr, 0.0003 part of Be) to smelt at a certain temperature , specifically, the melting temperature is 740 °C;
[0044] (2) After the charge is all melted, add a refining agent at 740°C, carry out refining treatment on the melt, and remove the slag after holding for 20 minutes;
[0045] (3) refining and degassing the refined melt in a vacuum state, the temperature is controlled at 740° C. for 20 minutes, followed by semi-continuous casting, and an aluminum alloy round ingot is obtained after cooling;
[0046] (4) the ingot-forming aluminum alloy processed by the above steps is subjected to heat preservation and homogenization ...
Embodiment 2
[0055] This embodiment provides a preparation method of an aluminum alloy super-large ring forging, and the preparation method includes the following steps:
[0056] (1) Control the above-mentioned aluminum alloy (in terms of weight per hundred parts of aluminum alloy, composition: 0.1 part of Cu, 1.8 part of Mg, 5.0 part of Zn, 0.1 part of Ti, 0.2 part of Cr, 0.0003 part of Be) to smelt at a certain temperature , specifically, the melting temperature is 740 °C;
[0057] (2) After the charge is all melted, add a refining agent at 740°C, carry out refining treatment on the melt, and remove the slag after holding for 20 minutes;
[0058] (3) refining and degassing the refined melt in a vacuum state, the temperature is controlled at 740° C. for 20 minutes, followed by semi-continuous casting, and an aluminum alloy round ingot is obtained after cooling;
[0059] (4) the ingot-forming aluminum alloy processed by the above steps is subjected to heat preservation and homogenization ...
PUM
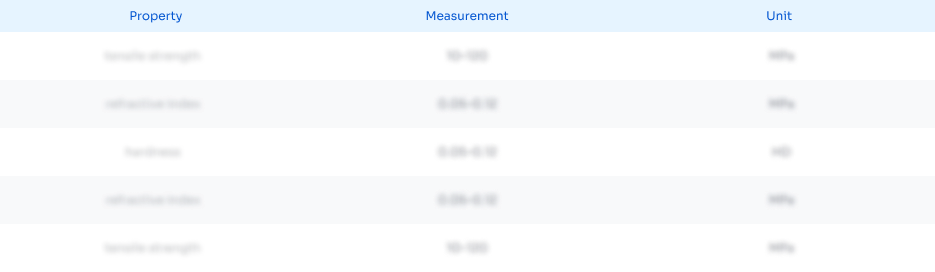
Abstract
Description
Claims
Application Information

- R&D
- Intellectual Property
- Life Sciences
- Materials
- Tech Scout
- Unparalleled Data Quality
- Higher Quality Content
- 60% Fewer Hallucinations
Browse by: Latest US Patents, China's latest patents, Technical Efficacy Thesaurus, Application Domain, Technology Topic, Popular Technical Reports.
© 2025 PatSnap. All rights reserved.Legal|Privacy policy|Modern Slavery Act Transparency Statement|Sitemap|About US| Contact US: help@patsnap.com